Dimensional inspection to confirm that products and parts are finished to the specified dimensions is an important process in manufacturing. In the past, human visual inspection was the mainstream, but it was time-consuming and time-consuming, and inspection errors occurred. Currently, automation using dimensional inspection equipment is progressing, and it is becoming possible to realize dimensional inspection efficiently and without mistakes.
In this column, we will introduce the mechanism and merits of dimensional inspection by dimensional inspection equipment, and points to consider when introducing dimensional inspection equipment.
If You Are Planning To Introduce Dimensional Inspection Equipment:
- You want to reduce costs by saving labor and manpower.
- You want to reduce human error and improve quality value
- You are not sure which manufacturer’s dimensional inspection equipment is most efficient
If you are considering the automation of dimensional inspection using image processing, you can also take advantage of our “Image Processing Laboratory,” a one-stop service that handles everything from rule-based image processing to AI-based image processing.
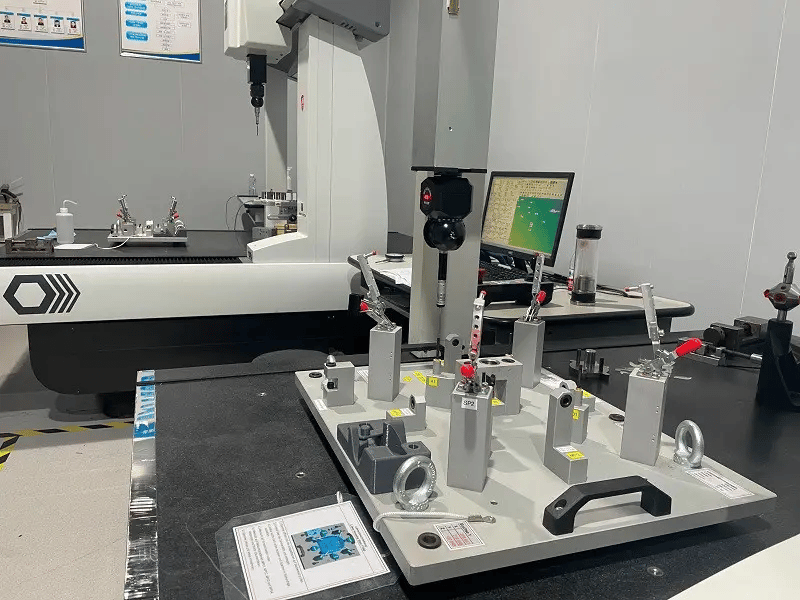
What is dimensional inspection?
First, let us review the purpose and method of performing dimensional inspections.
(1) Purpose of dimensional inspection
① Confirming that the product is made according to specifications
Manufacturers are obligated to ensure that the quality of their products and parts are manufactured according to specifications. To this end, dimensional inspections are conducted to confirm that products and parts are finished according to drawings and specifications. If a product is determined to be defective as a result of the dimensional inspection, the quality of the product is guaranteed by excluding the defective product from the list of good products.
② Maintain and improve the quality of products
Manufacturers must strive to maintain the quality of the products and parts they produce. Quality can be maintained by continuously conducting and checking dimensional inspections. It is also important to continuously improve quality by repeating the cycle of analyzing defective products found by dimensional inspection, identifying the causes of occurrence, and making improvements at the manufacturing site.
(2) Methods Of Dimensional Inspection
Methods of dimensional inspection can be broadly divided into the following three patterns:
- Measuring tools
This is a method in which dimensional inspections are performed manually using measuring tools such as calipers, micrometers, and dial gauges. The disadvantage of this method is that it is inefficient and the measurement results may vary depending on the skill of the person performing the measurement.
- Measuring equipment
This is a method of dimensional inspection using measuring equipment operated by human hands. By using measuring equipment such as projection machines and image dimensional measuring machines, dimensional inspection can be performed with higher precision than dimensional inspection with measuring tools. However, it is not a highly efficient method because it requires a person to set and operate the measuring object, and is not suitable as a method for measuring items manufactured in large quantities and at high speed.
- Dimensional inspection equipment
This is a method of performing unattended dimensional inspection by introducing a dimensional inspection system that operates automatically. An automatic dimensional inspection system is constructed by combining a conveyor system and an image processing system. Compared to other methods, the introduction cost is higher, but dimensional inspections can be performed quickly and accurately.
2. Mechanism of dimensional inspection equipment
Generally, dimensional inspection equipment uses image processing for dimensional inspection. The following is a brief overview of how dimensional inspection by image processing is performed.
- Edge detection
The first step in dimensional inspection by image processing is edge detection. Edge refers to a border area in an image where there is a significant change in the shade of color.
Thus, edge detection clarifies the shape of the object to be measured by detecting areas where the color shade changes significantly. However, since the actual measurement object may not have a clear shape or the image may be too blurred to detect the boundary well, pre-processing must be performed on the image to enhance the boundary.
Please refer to this article for a detailed explanation of edge detection if you are interested.
- Various measurements based on edges
Various dimensional measurements are made using edges detected by edge detection.
Various dimensional measurements are instantly performed based on edges, such as measuring the distance from edge to edge, measuring angles, and calculating and measuring the coordinates of intersections between edges, to determine whether the product is within dimensional tolerances.
In this way, dimensional inspection by dimensional inspection equipment automates and speeds up dimensional measurement by instantly detecting edges and performing various types of measurement.
3. Applications Of Dimensional Inspection Equipment
The following is a list of applications for dimensional inspection equipment:
(1) Confirmation of workmanship
The inspection system measures whether manufactured products and parts are finished according to drawings and specifications. There are two types of dimensional inspections: interim inspections conducted during the manufacturing process and finished product inspections conducted after manufacturing. Defective products that are determined to be out of specification as a result of dimensional inspection are eliminated from the production line, and only good products that pass dimensional inspection are sent to the next process or shipping process.
(2) Positioning
Dimensional inspection equipment is also used for positioning in the manufacturing process. The position of parts, films, labels, and other workpieces is identified by dimensional inspection, and the position information is transmitted to robots and other devices for accurate assembly operations.
4. Advantages of Introducing Dimensional Inspection Equipment
There are three advantages to installing dimensional inspection equipment:
(1) Reduction of inspection time
The introduction of dimensional inspection equipment enables instant dimensional inspections using image sensors. Therefore, the inspection time can be significantly reduced compared to manual inspection. The inspection process can become a bottleneck if inspections are performed manually, but by introducing dimensional inspection equipment, dimensional inspections can be performed at the same production speed as other processes.
(2) Elimination of human error
When dimensional inspections are performed manually, there is no small amount of variation due to differences in the skills of the persons in charge of inspections. In addition, if a worker is working continuously for a long time or is in poor physical condition, he or she may lose concentration and make an inspection error, resulting in the outflow of defective products. However, with dimensional inspection equipment, dimensional inspections are performed based on pre-set pass/fail criteria, thus ensuring stable quality. In addition, the machine can continue to perform dimensional inspections accurately and without fatigue due to its operation.
(3) Reduction of labor costs
Once a dimensional inspection system is installed, the only human work required is the operation and maintenance of the system, thereby reducing the number of inspectors. Rather than employing a large number of inspectors, it is less risky to introduce dimensional inspection equipment that can be used universally.
5. points to keep in mind when introducing dimensional inspection equipment
The following are points to be considered when introducing dimensional inspection equipment.
(1) Selection of the most suitable camera
An essential part of building a dimensional inspection system is a camera. Since the camera processes images of what it sees to measure dimensions, what can be measured and the accuracy will vary depending on the camera’s performance. Be sure to select a camera based on the following four selection points.
① Number of pixels
The number of pixels is related to the accuracy of dimensional measurement. Select a camera with the optimal number of pixels considering the size of the object to be measured and its dimensional tolerance.
② Color camera or B/W camera
If the boundary line of the object to be measured does not easily change from light to dark, it may be better to use a color camera since edge detection will be difficult. Decide whether to use a color or B/W camera after considering the object to be measured and conditions.
③ Transfer speed
Some cameras used in image processing have high transfer speeds. If the production line speed is high, the transfer speed should also be taken into consideration when selecting a camera.
④ Size
Cameras may have the same performance but different sizes. If the space for installing a camera is limited, it is better to select a smaller camera.
(2) Selection of optimal lighting
Although the camera tends to be the focus of attention in dimensional inspection, the selection of lighting that projects the workpiece is also important for detecting the correct shape. The following three points should be considered when selecting lighting.
① Illumination Method
There are three types of illumination methods: direct reflection type, diffuse reflection type, and transmission type. The regular reflection type is characterized by its ability to clearly detect uneven surfaces of workpieces, such as metal surfaces, where illumination is easily reflected. The diffuse reflection type can detect workpieces with no problem even if they are covered with transparent tape or other materials that would reflect the illumination.
The transmissive type can detect workpieces that cannot be detected by reflection from the front side by irradiating transmitted light from the opposite side of the camera.
Which of these three types should be used should be determined based on the shape of the workpiece and the inspection application.
(2) Illumination color
The color of illumination is selected according to the color and background of the workpiece to be inspected. If a color camera is selected, the color of illumination is basically white. For a monochrome camera, however, illumination should be of a color that allows clear detection of the boundary lines of the workpiece when the workpiece is illuminated.
(3) Illumination type
Illumination types include ring type, dome type, bar type, backlight type, and coaxial epi-illumination type. Although the backlight type is often used for dimensional inspections, each type has its own application, so it is necessary to select the type that is best suited for the application.