Manufacturing cost is a necessary number for cost control in the manufacturing industry. This article provides an overview of manufacturing costs, how to classify them as direct or indirect costs, and the differences between cost items such as material costs, labor costs, and expenses, as well as the methods and procedures for calculating manufacturing costs and costing.
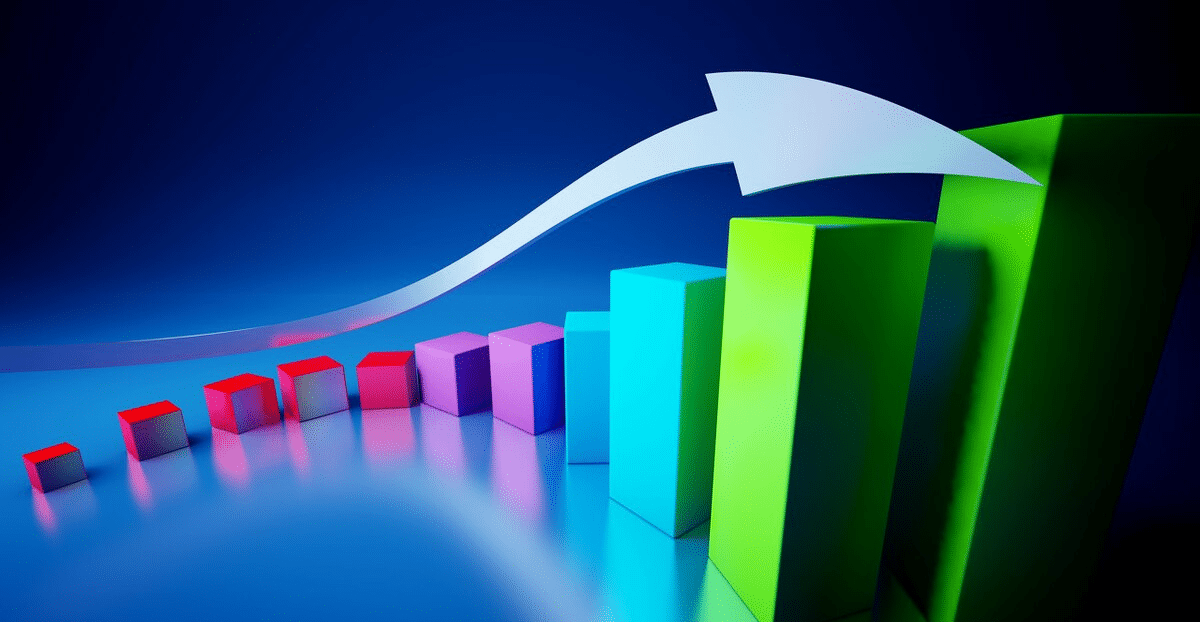
Manufacturing Cost Is All Costs Involved In Manufacturing
Manufacturing cost is the sum of all costs incurred in making a product in the manufacturing industry. In the manufacturing industry, raw materials are purchased, products are made, and the finished products are sold. Various costs are incurred in the manufacturing process, including the materials used to make the product, labor costs to obtain the labor needed to make the product, and other expenses. The total cost incurred in making these products is the manufacturing cost.
Companies that sell their products on their own also spend on various sales activities, such as sales activities and advertisements, in order to sell their products as well as to manufacture them. However, only the expenditures incurred in making the product are related to manufacturing costs. Expenditures for sales activities spent for the purpose of increasing product sales are not related to manufacturing. If you select only the amount of all expenditures related to manufacturing and calculate the total, you can clarify the manufacturing cost.
How to classify manufacturing costs
There are two main methods of classifying manufacturing costs: one is to divide them into direct costs and indirect costs, and the other is to divide them by the type of expense incurred. It is necessary to properly divide the costs by the amount that can be determined which product was used to make the product, the amount of the expense portion that is difficult to understand because the classification is ambiguous because it is used for several products, and the amount that can be divided by the purpose for which the expense was used.
Categorize By Direct And Indirect Costs
Direct costs are expenses that are tied to the manufacture of a certain product. They can be easily separated because their relationship to the product is easy to understand. Conversely, indirect costs are expenses that are not tied to the manufacture of a fixed product and are difficult to determine. By first dividing them into direct and indirect expenses, which are easy to divide, and then further dividing them into more detailed categories, it is possible to grasp which part of the product is related to which part of the manufacturing process.
Direct Manufacturing Expenses
Direct manufacturing costs are the expenditures and amounts directly related to product manufacturing. Since we can clearly identify the products involved and the quantities used to make them, we can see that as the number of products manufactured increases, direct manufacturing costs also increase. Direct manufacturing costs can be further divided into three categories: direct material costs, direct labor costs, and direct expenses.
For example, “direct material costs” include expenditures for purchasing raw materials necessary for manufacturing products, such as lumber, screws, plastic, glass, and other materials needed to make furniture, as well as expenditures for purchasing goods that are consumed in the manufacturing of products. If we can analyze “direct material costs,” we can reduce wasteful costs by improving the efficiency of manufacturing methods, thoroughly managing inventory, and so on.
Direct labor costs” are expenditures for wages, bonuses, and benefits for employees working in the factory who are in charge of making a certain product. It directly reflects the wages and overtime paid to employees who work on a defined product. This figure indicates a state of waste if employees are working too much overtime for the amount of product actually produced. To eliminate waste in “direct labor costs,” it is important to improve efficiency by reviewing work flow.
Direct labor costs” refer to expenditures that are not divided into material and labor costs. Depreciation of machinery related to the manufacture of a certain product, outsourced processing costs if part of the product manufacturing is outsourced, and travel expenses for business trips for product development are also “direct expenses. If there are parts that are too costly to manufacture in-house because the equipment and technology are not suitable for your company, you may be able to reduce costs by outsourcing the part manufacturing rather than forcing your company to manufacture the part in-house.
Manufacturing Overhead
Manufacturing overhead is an expense that is not directly related to a single product, but is related across several products, as opposed to direct expenses, which represent expenses directly related to the manufacturing of a product. Indirect costs, like direct costs, can be divided into three categories: indirect material costs, indirect labor costs, and indirect expenses. Indirect material costs include expenditures for the purchase of materials used in a wide range of products.
Indirect material costs can be further divided into three categories: auxiliary material costs, factory supplies costs, and consumable tools and equipment costs. Supplementary materials, such as fuel used to run machinery, paint and adhesives used in several products, etc., for which the amount of materials used for each product is not known, are classified as “Supplementary materials. Tools used for work, such as screwdrivers, desks, chairs, etc., can be classified as “consumable tools, furniture, and fixtures”.
Indirect labor costs” are expenditures for wages, bonuses, and legal welfare costs for employees who are not actually making products in the factory, but are indirectly involved in the production of several products in a variety of tasks, such as transportation and machine maintenance in the production management department, administrative department, and even the quality control department. Wages incurred during standby time rather than during product manufacturing are also classified as “indirect labor costs.
Indirect expenses are the amounts used in the production of some products other than the above “indirect material costs” and “indirect labor costs. Indirect costs include expenses that affect the entire manufacturing process, such as office supplies, communications and transportation, and meeting expenses, as well as expenses for electricity and repairs to factory equipment. Indirect expenses are difficult to manage because the percentage of each product used in the production process is not clearly defined. Profit improvement can be expected through management efforts such as overall savings, or by aiming for greater efficiency through capital investment and digitalization.
Classifying Expenses by Type of Incurred Expenses
Another method is to classify expenditures incurred during manufacturing into three categories by the purpose of the expenditure: material costs, labor costs, and expenses. By classifying expenditures, it is possible to see where too much money is being spent.
Material Cost
Material cost in manufacturing cost includes the cost of raw materials used in the production of products. Various expenditures such as raw material costs for purchasing materials for products, purchased parts as parts for products, fuel required to run equipment used in product manufacturing, low-cost tools and other consumables used in factories, and large equipment and tools fixtures are material costs. Among manufacturing costs, raw materials are determined to be those items that are used and lost in the making of a product. Expenditures for machine oil, etc., which decrease during manufacturing even if the amount used is not known, as well as those that are used in fixed quantities during product manufacturing, are included in the cost of materials as consumables.
Labor Cost
Labor costs in manufacturing costs are wages and other expenditures paid to employees working in the product manufacturing department and other employees performing work related to product manufacturing. Labor costs include expenditures for wages such as base salary and overtime, bonuses, commuting allowances, family allowances, rent subsidies, and other allowances, miscellaneous wages paid to part-time and casual workers, legal welfare expenses that are the company’s portion of social insurance, and reserve funds for retirement payments. Labor costs are expenditures for part-time, casual, and permanent employees in manufacturing and other industries that make products. In industries such as retail and sales, these labor costs are mainly classified as selling expenses, not labor costs.
Expenses
Expenses are those expenses other than material and labor costs that are included in manufacturing costs. Direct expenses are clearly related to product manufacturing, while indirect expenses are characterized by the fact that it is difficult to see how they are related to actual product manufacturing. These expenses include subcontracting costs when parts are outsourced, rent for factory land and buildings, depreciation of machinery and equipment, inventory depletion costs, lease costs for office equipment, electricity, water, and communication costs, and so on. Even if it is not clear that the expenses are related to the production of products, it is possible to classify expenses that are indispensable to the operation of the factory as expenses.
How Manufacturing Costs Are Calculated?
The manufacturing cost calculation method is obtained from the total of direct costs and indirect costs divided into the above six types. In addition, the sum of these amounts is the “current period’s total manufacturing cost,” which represents the total amount spent on product manufacturing in the current period. In addition, it is possible to calculate the manufacturing cost by confirming the figures of “Inventory amount of materials and work in process at the beginning of the period” and “Inventory amount of materials and work in process at the end of the period”.
This calculation is done by subtracting the cost of work in process and unused materials at the end of the period from the sum of the starting work in process inventory and the total cost of manufacturing for the period. Below is the formula for manufacturing cost.
“Cost of manufacturing products for the current period = Inventory of work-in-progress at the beginning of the period + Total manufacturing costs for the current period – (Inventory of work-in-progress at the end of the period + Cost of unused materials)”
There are two methods of cost accounting
There are two types of calculation methods for cost accounting: manual calculation and system-based calculation. When doing it manually, it is necessary to reliably calculate each step of the three-step calculation, but using the system makes it possible to calculate easily in a short time.