In the dynamic and competitive landscape of manufacturing and quality management, organizations strive for excellence by constantly identifying and mitigating potential risks. One powerful tool that has emerged to address risks and ensure robust processes is the Process Failure Mode and Effects Analysis (PFMEA). PFMEA is a systematic approach used by manufacturing and quality professionals to proactively identify and assess potential failure modes, their effects, and the corresponding preventive and corrective actions within a manufacturing process. With this post, we break down the fundamental aspects of PFMEA, exploring its purpose, methodology, and the benefits it brings to manufacturing and quality management. By understanding the intricacies of PFMEA, organizations can enhance their ability to prevent failures, improve overall product quality, and drive customer satisfaction.
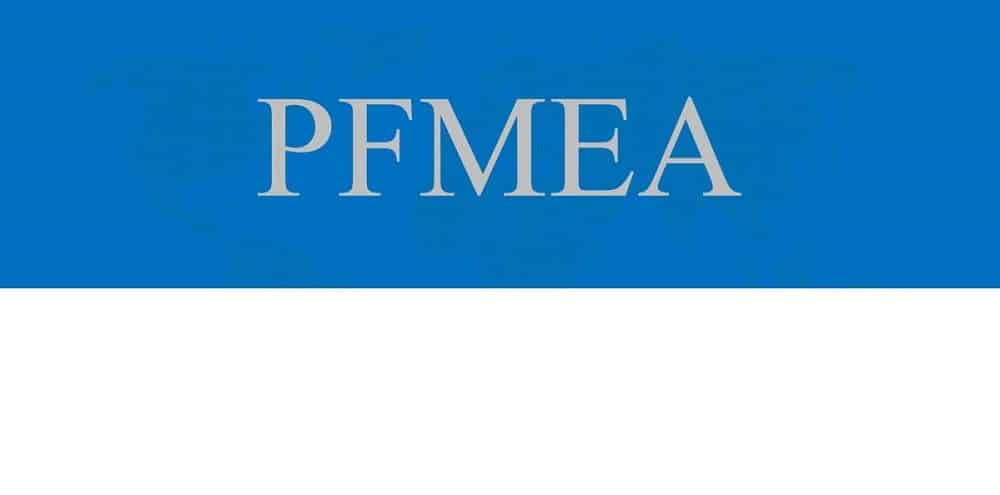
What is PFMEA in Manufacturing?
PFMEA stands for Process Failure Modes and Effects Analysis. It is a structured approach used in manufacturing and various other industries to identify and prioritize potential failure modes within a manufacturing or business process and assess their potential effects on the product or service being produced. The primary goal of PFMEA is to proactively identify and mitigate risks to improve product or process quality and reliability.
Here’s a breakdown of the key components of PFMEA in manufacturing:
- Process: This refers to the specific manufacturing or business process that is being analyzed. It could be any process within a company, from product assembly on a factory floor to administrative tasks in an office.
- Failure Modes: These are the ways in which the process can fail or go wrong. Failure modes could be related to equipment malfunctions, human errors, material defects, or other factors that may lead to problems in the process.
- Effects: Effects are the consequences or outcomes of each identified failure mode. These can include defects in the product, customer complaints, safety hazards, increased production costs, or any other negative impact on the process or end product.
- Severity (S): This is a numerical rating assigned to each failure mode to indicate the seriousness of its potential consequences. The scale typically ranges from 1 to 10, with higher numbers indicating more severe consequences.
- Occurrence (O): This rating assesses the likelihood or frequency of each failure mode occurring. It is also usually rated on a scale from 1 to 10, with higher numbers indicating a higher likelihood of occurrence.
- Detection (D): This rating assesses how likely it is for the failure mode to be detected before it reaches the customer or causes significant problems. Like severity and occurrence, it is typically rated on a scale from 1 to 10, with higher numbers indicating a lower likelihood of detection.
What is PFMEA in Quality?
In the context of quality management, PFMEA (Process Failure Modes and Effects Analysis) is a structured methodology used to assess and manage potential failure modes within a manufacturing or business process, with a primary focus on their impact on product or service quality. PFMEA is a critical tool within the broader framework of Total Quality Management (TQM) and Six Sigma.
Here’s how PFMEA relates to quality management:
- 1. Identification of Quality Risks: PFMEA helps identify potential risks and failure modes that could lead to defects or quality issues in a product or service. These failure modes can encompass various aspects, including design, materials, equipment, processes, and human factors.
- 2. Severity of Quality Impact: Within PFMEA, one of the key components is the severity rating (S), which assesses the seriousness of the potential consequences on product or service quality if a failure mode were to occur. This helps prioritize and address the most critical quality risks.
- 3. Occurrence of Quality Issues: The occurrence rating (O) in PFMEA evaluates the likelihood or frequency of a particular failure mode occurring and affecting product quality. Identifying high-occurrence failure modes is crucial for quality improvement efforts.
- 4. Detection of Quality Defects: The detection rating (D) assesses how likely it is for the failure mode to be detected before it reaches the customer or impacts product quality. Higher detection ratings indicate a lower likelihood of detecting the quality issue in advance.
- 5. Risk Prioritization: By calculating the Risk Priority Number (RPN), which is the product of severity, occurrence, and detection ratings, organizations can prioritize which failure modes pose the greatest quality risks and require immediate attention.
- 6. Quality Improvement Actions: PFMEA helps organizations develop action plans to mitigate or eliminate high-risk failure modes. These actions may involve process improvements, quality control measures, design changes, or other strategies to enhance product or service quality.
- 7. Continuous Quality Monitoring: After implementing mitigation actions, PFMEA should be an ongoing process. Organizations should continuously monitor the process and review the PFMEA to ensure that the actions taken are effective and that new quality risks are addressed promptly.
PFMEA in quality management is a systematic approach to prevent and manage quality-related issues by proactively identifying potential failure modes, evaluating their impact, and taking corrective and preventive actions. It plays a crucial role in ensuring that products or services meet or exceed customer expectations and in maintaining a strong commitment to quality throughout an organization.
The Steps Involved in PFMEA
The PFMEA process typically involves the following steps:
- Assemble a Cross-Functional Team: Bring together a team of experts from various departments (e.g., engineering, manufacturing, quality control) to collaborate on the analysis.
- Identify Process Steps: Break down the process into individual steps or components.
- Identify Failure Modes: For each process step, brainstorm and list all possible failure modes that could occur.
- Determine Severity, Occurrence, and Detection Ratings: Assign numerical ratings to each failure mode based on its severity, occurrence, and detection factors.
- Calculate Risk Priority Number (RPN): The RPN is calculated by multiplying the severity, occurrence, and detection ratings. This number helps prioritize which failure modes require the most immediate attention.
- Prioritize and Implement Mitigation Actions: Focus on the failure modes with the highest RPN values and develop action plans to mitigate the risks associated with these modes. These actions may include process improvements, redesigns, or additional quality control measures.
- Monitor and Review: Continuously monitor the process and periodically review the PFMEA to ensure that the implemented actions are effective and that new risks are addressed.
By systematically analyzing and addressing potential failure modes, PFMEA helps organizations improve the quality, reliability, and safety of their products or services, ultimately leading to greater customer satisfaction and reduced production costs.