Various types of quality inspections are carried out at manufacturing sites. Pinhole inspection is also a type of quality inspection used in the field of manufacturing, but few people may understand how it works. In this article, we will explain the mechanism, types, and usage scenarios of pinhole testing.
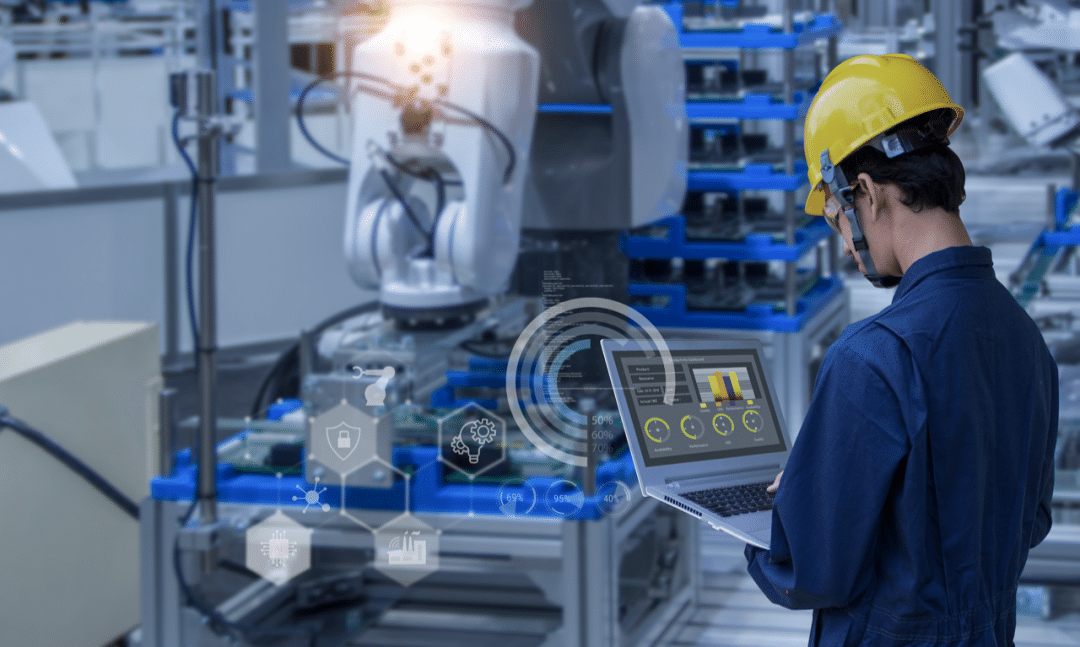
What Is A Pinhole?
A pinhole is a small defect that is so small that it is not visible. A pin means a needle, a hole means a hole, and a defect that looks like a small hole drilled by a needle is called this. Whether it’s construction, food, or pharmaceuticals, pinholes are perceived as a headache in a variety of industries.
For example, in the building and construction industry, a pinhole is a small hole that appears on the surface of a coating film. In painting work, paint is applied to the object using a special roller. At this time, the hair of the roller may pull the paint, and air bubbles may form. When these bubbles break, holes are created.
In industry, a small defect in a welded area is called a pinhole. When gas generated inside metal melted at high temperatures is ejected, extremely small holes and rises are formed at the welding site. Pinholes can also occur in everything from paper and film to vinyl-coated wires, plastic packaging, food cups, and liquid crystals.
As mentioned earlier, pinholes are small defects that are invisible to the eye, and there are many cases where they are not noticed by inspection alone. Even the smallest defects can have a variety of negative effects on consumers, so many industries are working to combat pinholes.
Why Is Pinhole Inspection Important?
A pinhole test is a test to check for the presence or absence of pinholes. Different companies and industries use different inspection methods, but it’s true that every company is committed to finding pinholes. So why is pinhole inspection so important?
Pinholes can cause corrosion or damage. Even if the hole is originally very small, there is a risk of it expanding due to corrosion or damage. Such areas are more vulnerable than others and can cause significant damage.
For example, let’s say you have a pinhole in your food packaging. If the pinhole widens during the packaging and transportation process, the contents may leak outside. In addition, the widening of the hole may make it easier for contaminants to enter from the outside, which may affect the contents.
If the food in the packaging is contaminated, the consumer who ate it may suffer health hazards. In some cases, it may cause serious health damage and lead to major litigation. For companies that handle food, this is a fatal problem that will affect their business continuity in the future.
In addition, if a pinhole occurs in the painting of a building, the interior may corrode, adversely affecting the frame that is the skeleton of the building. As a result, problems such as reduced durability of buildings and leaks may occur.
As you can see, pinholes are a flaw that needs to be eradicated in any industry. That is why in the world of manufacturing, it is necessary to properly conduct pinhole inspections and detect defects at an early stage.
How Pinhole Testing Works
There are several types of pinhole inspections, including visual inspection, airtightness, penetrant inspection, ultrasonic inspection, radiographic inspection, discharge inspection, and visual inspection. The most commonly used type of traditional pinhole inspection is penetrant testing. This is an inspection in which a test solution with good penetration is applied to the surface of the object and the presence or absence of pinholes can be visually confirmed by the development process.
There are several types of penetrant testing, but the most commonly used method is called solvent removal stain penetrant testing. The surface is cleaned by pretreatment, penetration treatment is performed, and after the penetrant is removed, it is developed and inspected.
However, penetrant inspection takes a lot of time and effort to preprocess, and it is difficult to inspect depending on the material of the object. Therefore, various methods have been born, such as inspection to detect pinholes by irradiating light and visual inspection using AI.
Main Inspection Methods For Pinholes
Since we have just introduced penetrant testing, which has been commonly used in the past, we will explain other methods here.
Visual inspection is literally an inspection that detects pinholes visually. The object is checked with human eyes for defects. Since it may not lead to a discovery just by looking at it with the eyes, a loupe is sometimes used.
Airtightness inspection is mainly used to detect defects in containers, and there are two types. This includes a “submersion test” in which nitrogen is injected into a container and placed in a water tank to check whether bubbles are emitted from the inside, and a “foaming test” in which a foaming spray is applied to the container and nitrogen is sent into the container with a nitrogen cylinder to check for foaming.
Discharge-type inspection is a method in which the part that is considered to be defective is pinched with an electrode and a voltage is applied to check for the presence of pinholes. If there is a hole, a discharge arc will occur from the electrode.
Visual inspection using a camera mainly uses a CCD camera. The product flowing through the line is photographed with a CCD camera and the information is sent to the image processing device. If it determines that it matches the characteristics of the pinhole, it will alert you with an alarm.
Ultrasonography is primarily used to detect container defects. Compressed air is pumped into the vessel, and the receiver detects the ultrasonic waves generated when air is ejected through a small hole. The volume of ultrasonic waves emitted differs depending on the size of the hole, from which the size of the hole can also be determined.
Main Use Cases Of Pinhole Inspection
Pinholes are defects that can happen to anything. Therefore, the use of pinhole inspection is diverse. It is used not only for painting buildings and concrete walls, but also for plastic packaging of food and medicine.
Various pinhole detectors have now been released. Whether it’s one that specializes in detecting defects in plastic cladding, one that specializes in inspecting food and medicine containers, or one that detects insulator defects, each company must use inspection equipment that matches their products.
Pinholes are minor flaws, but when they occur, they can severely erode a company’s credibility. To prevent this from happening, companies must do their utmost to find pinholes.
There are various methods for pinhole inspection, including penetrant inspection. When selecting the one that suits your company, it is a good idea to consider the judgment accuracy and the benefits that can be obtained.