In the manufacturing industry, if the manufactured products are shipped without checking, there is a possibility that the trust of business partners and end users will be greatly damaged when defective products occur. Therefore, the indispensable task is the inspection of products performed in the manufacturing process.
This time, after explaining the purpose of inspection in manufacturing, we will explain the main flow of the inspection process, the advantages and disadvantages of inspection, and the automation of inspection that eliminates the disadvantages and realizes operational efficiency and productivity improvement.
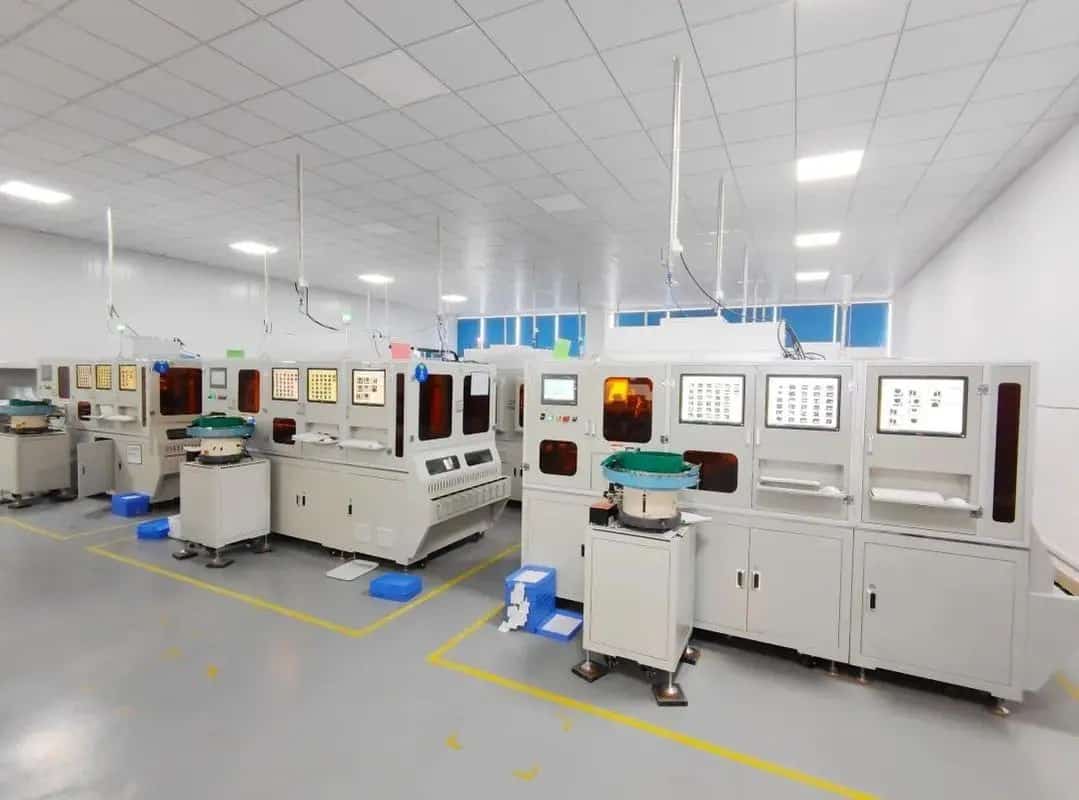
Purpose of Quality Inspection in the Manufacturing Process
There are several possible purposes for inspection in the manufacturing process, but the following two are the most important.
Reduction of defective products, quality assurance
No matter how carefully the product is manufactured, it is difficult to reduce the occurrence of defective products to zero. However, if nothing is done, there is an increased risk that many defective products will be produced.
Of course, defects caused by accidents during shipping cannot be suppressed at the manufacturing stage, but defects that occur at the manufacturing stage must be found before shipping as much as possible. One of the purposes of inspection in the manufacturing process is to reduce defective products before shipping, which also leads to guarantee of product quality to business partners and end users.
Maintaining and improving product quality
If a defective product can be detected in the manufacturing process by visual inspection, it will be easier to identify the cause of the defect. As a result, it will be possible to take measures to prevent defective products such as equipment improvement and personnel training, and it is expected that product quality will be maintained and improved.
Main Process of Quality Inspection
Now, let’s take a brief look at the overall flow of the inspections that are actually performed in the manufacturing process, and then explain the details of each.
Generally, the following four inspections, “acceptance inspection”, “in-process inspection”, and “final inspection”, are performed in the manufacturing process.
“Acceptance inspection” to check if there are any problems with the raw materials and materials that have arrived for use in the manufacture of products.
“In-process inspection” that is performed by periodically extracting products in the middle of production from the production line
“Final inspection” to check whether the finished product meets the standards required by the business partner
Acceptance Inspection
Acceptance inspection is the first step in the manufacturing process. The contents and the main methods are as follows.
What is acceptance inspection?
Acceptance inspection is an inspection conducted when raw materials and materials that are indispensable for manufacturing products arrive, and it is checked whether each of them conforms to quality standards. Even if there is no problem in the manufacturing process, if the raw materials and materials that arrive are defective, we cannot manufacture good products.
Insufficient acceptance inspections can be more burdensome and costly for later inspections. Conversely, it is possible to optimize the operation of the production line by conducting an acceptance inspection and repelling defective raw materials and materials in advance. As a result, it will have the effect of reducing the burden on personnel and costs.
Acceptance inspections may also include inspections to determine if it is okay to purchase raw materials or materials from a particular supplier and store them in your factory or warehouse. This is an inspection called “purchase inspection” in the acceptance inspection.
Main Methods of Acceptance Inspection
Acceptance inspections can be broadly divided into two types: “inspections for deciding the purchase of raw materials and materials” conducted outside the company and “inspections for warehousing in factories and warehouses” conducted internally.
There are no rules on the inspection method for either, but if you discuss external inspections with the supplier and reach a consensus, you can reduce the risk of developing trouble. Basically, it is best to make a decision in light of the standards required by the business partner who delivers the product.
As a specific inspection method, sampling inspection or 100% inspection of raw materials and materials is mainly performed visually. Although 100% inspection can bring defective products as close to zero as possible, it is time-consuming and costly, so unless there are no defective products, it is common to perform inspections by sampling.
In raw material inspection, we perform inspections based on raw material standards that have been agreed with our suppliers, such as “appearance,” “odor,” “property,” and “instrumental analysis.” In material inspection, “function” and “appearance” are carried out based on the material inspection standard.
By the way, all the responsibility for the raw materials and materials received at the end of the acceptance inspection shifts from the supplier to the receiving side, so even if a defect is detected after that, it is the company’s responsibility.
During Production Inspection
This is an inspection performed at the beginning of full-scale production of the product. It is called in-process inspection because it examines semi-finished products that have not been completed in the middle of the process.
What is During Production Inspection?
This in-process inspection is to periodically extract semi-finished products that are in the process of being manufactured on the production line, and check whether there are any defects at that stage and whether there are any problems by proceeding to the next process. Also called process inspection or intermediate inspection, it is performed to prevent defective products from proceeding to the next process.
If defective products cannot be detected in the middle of the process, there is an increased risk that defective products will continue to appear in the same location. Performing in-process inspections can help identify locations where defective products are likely to occur, so it can be said to be an inspection that greatly contributes to improving the manufacturing process.
Main Methods of During Production Inspection
The main methods of in-process inspection are “visual inspection” to check the appearance for scratches and stains, “foreign matter inspection” to check whether foreign matter is mixed in the product, and “filling” to check whether the content is appropriate. There are “quantity inspection”, “print display inspection” to check for label printing mistakes and stains, and “functionality confirmation inspection” to check whether the product is operating normally.
Batch Inspection
In the manufacturing process, mainly for cosmetics and quasi-drugs, Batch Inspection is performed before the contents are filled in individual containers.
Batch refers to the state of only the contents before filling in individual containers. In Batch, various methods are used to check whether the finished bulk conforms to the standard, and those that pass the inspection proceed to the filling and finishing process. It also has the purpose of quality control and safety control by keeping a record of inspection results and storing samples.
Main Methods of Batch Inspection
There are various inspection methods for bulk inspection, but the four main ones are as follows. Here, let’s take a look at each inspection method using cosmetics and quasi-drugs as examples.
Sensory test
A sensory test is a test performed using the five senses of a person, such as “sight,” “hearing,” “tactile,” “smell,” and “taste.” The appearance, color, odor, usability, etc. are actually inspected by human senses.
Physical Characteristic Inspection
This is an inspection to see the physical properties. We use a specific device to inspect “viscosity,” “hardness,” “breaking strength,” “density,” etc.
Inspection by quantitative and qualitative analysis
This is an inspection that uses specialized equipment to analyze bulk. The instruments mainly used are “liquid chromatography” for separating and analyzing substances contained in products, “gas chromatography” for separating and analyzing gases, “Fourier transform type infrared spectrophotometer” for irradiating and analyzing infrared rays on the substance to be measured, “atomic absorption photometer” for measuring how much light is absorbed when the luminous flux from the light source passes through the substance to be measured. and so on.
Microbiology testing
It is a test to check whether the batch is contaminated with microorganisms. Examine common bacteria such as E. coli and Grad Bacteria and fungi such as mold and yeast to see if bulk is contaminated.
After conducting these inspections and determining that the standards have been met, you can proceed to the next step.
Final Inspection
Final inspection aka Pre-Shipment Inspection is to inspect products that have been completed through the final process in accordance with the in-process inspection.
What is the Final Inspection?
Final inspection literally refers to an inspection performed to prevent defective products from reaching business partners and end users before the product is shipped. It is also called a Pre-Shipment Inspection because it is done at the time of shipment.
As with other inspections, if a single defective product is not allowed, a total inspection is performed, and in other cases, a sampling inspection is performed to determine whether the specified standards are met.
Main Methods of Pre-Shipment Inspection
Visual inspection is generally the main method of final inspection. We use standard samples that meet the standards as a product and limit samples to determine the limits of good and defective products, and conduct inspections by comparing them with finished products. Depending on the product, a checklist for inspection may be created and the inspection may be performed while checking one by one. At this time, there is a possibility that it will be overlooked by one person, so it is common to do it with 2 ~ 3 people.