What is a supply chain management system? What does it cover? Today, we will explore it through an article.
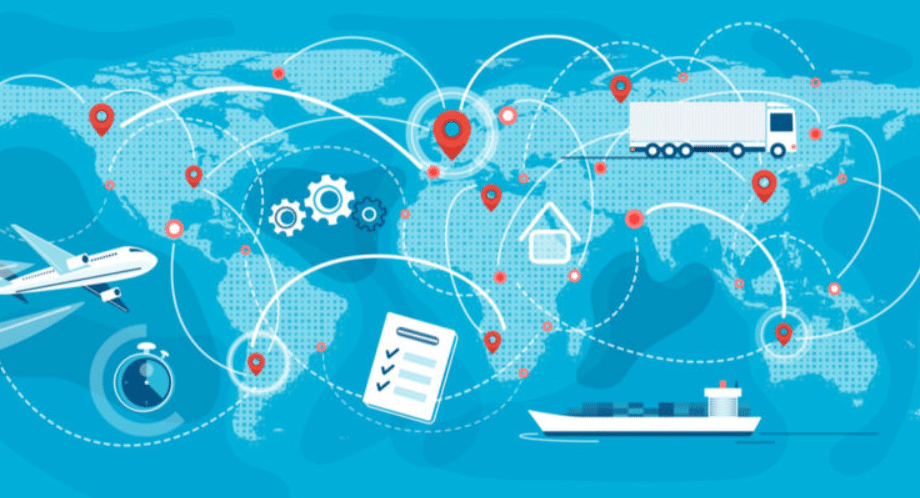
What is Supply Chain & Supply Chain Management?
Generally speaking, the supply chain is centered on the core enterprise, through the control of information flow, logistics, and capital flow, starting from purchasing raw materials, making intermediate products and complete products delivered to customers, and finally sending the products to consumers through the availability management by the sales network. Companies develop supply chains so that they can reduce costs and remain competitive in the business environment. Supply chain involves a series of steps to provide products or services to customers. These steps include moving and converting raw materials into finished products, transporting these products and distributing them to end users. The entities involved in the supply chain include manufacturers, suppliers, warehouses, transportation companies, distribution centers and retailers. The elements of the supply chain include all functions from receiving orders to meeting customer requirements. These functions include product development, marketing, operations, distribution, finance and customer service. Supply Chain Management (SCM) is a process that aims to improve the long-term performance of individual enterprises and the supply chain as a whole, coordinates the overall strategy of traditional business activities, and controls the operation of cross functional department boundaries within the company and across company boundaries among supply chain members.
Main Parts of Supply Chain Management
- Plan
Before the start of the supply chain, enterprises need carefully designed strategies to effectively manage each stage of the process, and make plans to determine the overall cost, profit and manpower required to complete the work. The person in charge of supply chain management weighs the advantages and disadvantages of various supply chain methods and makes subsequent plans for how to proceed. - Procurement
Enterprises rely on suppliers to provide different raw materials to manufacture their products. Finding appropriate high-quality materials at preferential prices enables enterprises to create quality, provide products with competitive prices, and establish a good reputation in the market. Procurement also involves selecting suppliers that provide services to operate specific business components. For example, hotel chains may require pool maintenance services, or manufacturers may require equipment maintenance. After selecting suppliers, enterprises need to manage these relationships and monitor processes, such as ordering, receiving inventory management, and payment authorization, to ensure that they meet enterprise standards. They also need to build trust and solid communication with suppliers. The higher the trust, the better the communication, the more likely the company will get better services and preferential conditions. - Manufacturing/Production
Manufacturing is the stage of supply chain management, in which enterprises transform raw materials (human or natural resources) into goods or services. According to customer needs and business objectives, the organization determines the most appropriate production process. Companies that produce large quantities of goods or services, such as headphones, light bulbs, or processed food, may choose the mass production model. Companies that make products according to customers’ preferences and personal needs usually choose different customized production processes. Manufacturing includes assembly, quality testing and packaging delivery. To ensure that products meet specified standards and manufacturing efficiency, supply chain professionals decide how best to perform the following tasks, including measuring production performance, storing data, managing production facilities, complying with regulations, and tracking worker productivity. - Customer service
Sales, after-sales, customer service, order and claim management, invoice, accounts receivable management and cash collection; - Logistics
Logistics includes transportation and warehousing. This component of supply chain management includes: processing customer orders, arranging delivery, distributing and shipping orders, invoicing and collection. - Return
This involves creating a smooth process for customers to return purchased products. Although the enterprise may have a strong quality control plan, defective or damaged products that customers want to return are inevitable. The equipment may fail and the faulty product may slip away.
The return process includes:
Evaluate the condition of returned products to determine whether they should be scrapped, refurbished or replenished
Authorized product return
Coordinate the transportation of replacement products
Issue refund