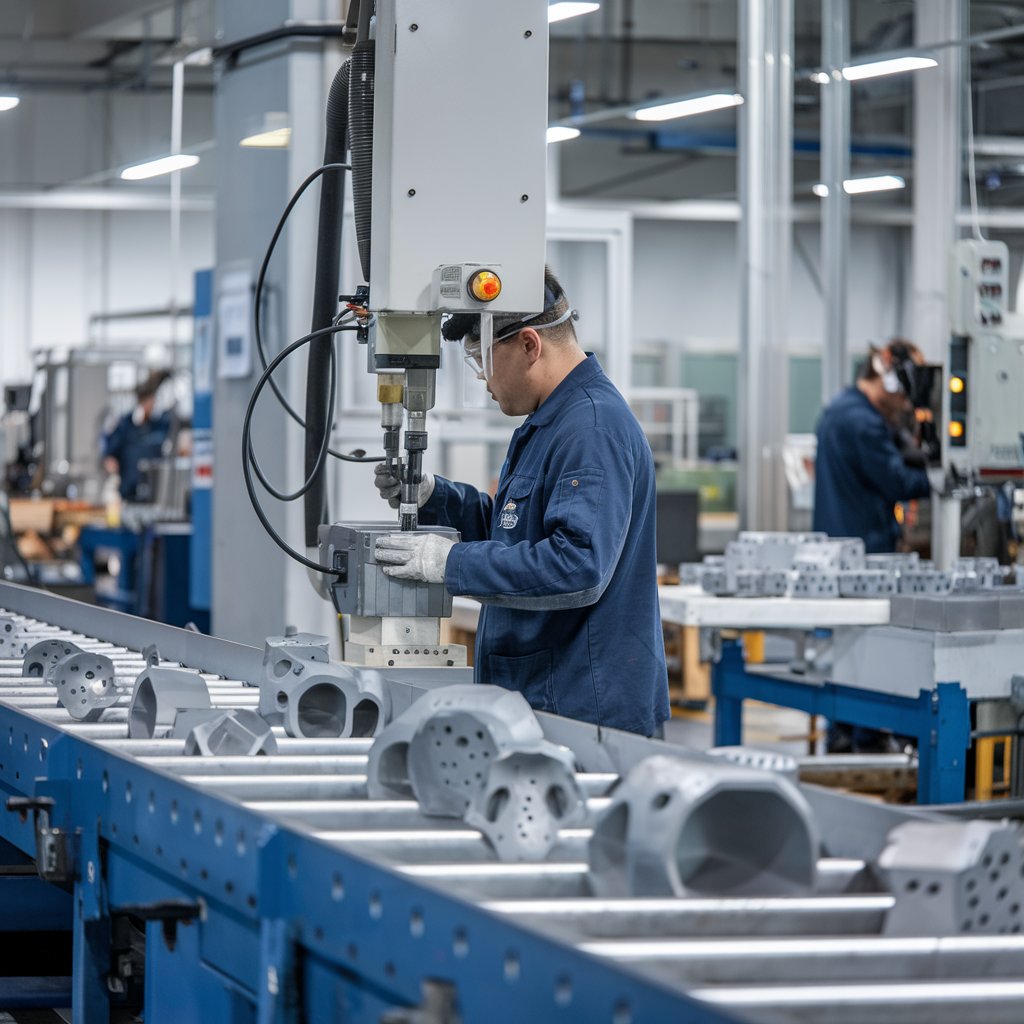
In manufacturing and quality control, the integrity and performance of materials and products are crucial. To ensure reliability, engineers use various testing methods to evaluate materials’ properties and detect flaws. These methods fall into two main categories: Destructive Testing (DT) and Non-Destructive Testing (NDT). While both are essential for ensuring product safety and compliance, they differ significantly in their approach, applications, and impact on the tested materials.
This blog will explore the key differences between destructive and non-destructive testing, their techniques, advantages, and ideal use cases.
Destructive Testing (DT)
Destructive testing involves applying forces or conditions that lead to the material’s failure or permanent damage. The primary goal is to understand the material’s limits, such as strength, durability, and resistance under specific conditions.
Common Techniques
1. Tensile Testing: Measures the strength of a material when stretched until it breaks.
2. Impact Testing: Assesses how much energy a material absorbs during sudden impact (e.g., Charpy or Izod tests).
3. Hardness Testing: Determines resistance to deformation (e.g., Brinell or Rockwell tests).
4. Fatigue Testing: Evaluates the material’s behavior under repeated stress cycles.
5. Fracture Toughness Testing: Measures resistance to crack propagation.
Advantages
· Provides precise and detailed data about material limits.
· Ideal for determining failure points and mechanical properties.
· Often required for certification and compliance in critical industries.
Limitations
· Destroys the tested specimen, making it unsuitable for high-value items.
· Limited to batch or sample testing rather than entire products.
· Time-consuming and often expensive.
Non-Destructive Testing (NDT)
Non-destructive testing evaluates materials or components without causing any damage, preserving their usability. NDT methods are used to identify internal or surface defects, assess structural integrity, and ensure product quality.
Common Techniques
1. Ultrasonic Testing (UT): Uses sound waves to detect internal flaws.
2. Magnetic Particle Testing (MT): Identifies surface and near-surface defects in ferromagnetic materials.
3. Radiographic Testing (RT): Uses X-rays or gamma rays to reveal internal discontinuities.
4. Visual Inspection (VI): Simple yet effective for surface-level checks.
5. Dye Penetrant Testing (PT): Highlights surface cracks using a penetrant dye.
Advantages
· Preserves the integrity of the tested material or product.
· Allows 100% inspection of critical components.
· Cost-effective for routine checks and large-scale quality control.
· Suitable for in-service equipment and assemblies.
Limitations
· May require specialized equipment and trained personnel.
· Interpretation of results can sometimes be subjective.
· Certain methods are material-specific (e.g., magnetic particle testing).
Key Differences Between DT and NDT
Aspect | Destructive Testing (DT) | Non-Destructive Testing (NDT) |
Material Damage | Causes permanent damage to the specimen. | Leaves the material intact and reusable. |
Scope | Sample-based; cannot test entire batches or products. | Can inspect entire components or assemblies. |
Purpose | Determines failure points and mechanical properties. | Detects defects and ensures integrity without damage. |
Cost | Often higher due to specimen destruction. | Generally more cost-effective for large-scale use. |
Applications | Research, product design, and certification. | Maintenance, quality assurance, and safety checks. |
Applications of DT and NDT
Destructive Testing
· Aerospace: Evaluating new materials for aircraft components.
· Construction: Determining the tensile strength of concrete or steel.
· Automotive: Testing crash-worthiness and material durability.
Non-Destructive Testing
· Energy: Inspecting pipelines, turbines, and boilers for defects.
· Manufacturing: Routine quality checks in production lines.
· Infrastructure: Assessing the health of bridges, buildings, and rail tracks.
Which Method Should You Choose?
The choice between DT and NDT depends on your specific objectives:
Use Destructive Testing if:
o You need to establish material limits.
o The testing is for research and development.
o The component is expendable or produced in large batches.
Use Non-Destructive Testing if:
o The component is high-value or critical to operations.
o You need to inspect finished or in-service products.
o Long-term maintenance or quality control is the focus.
Destructive and non-destructive testing both play vital roles in material evaluation and quality assurance. While destructive testing provides in-depth insights into material performance, non-destructive testing ensures safety and reliability without compromising the product’s usability.
By understanding the strengths and limitations of each method, businesses can make informed decisions about their testing strategies, ensuring both efficiency and compliance with industry standards. Whether in manufacturing, aerospace, or construction, selecting the appropriate testing method is key to maintaining high-quality, durable, and safe products.