In today’s globalized marketplace, ensuring the quality of your products is essential for maintaining customer trust and meeting regulatory standards. Whether you’re sourcing components internationally or producing goods locally, third-party quality control (QC) services play a critical role in verifying that your products meet required specifications before they reach the market. But how do you find reliable third-party QC providers, and what should you consider when choosing one? Let’s explore.
Why Third-Party Quality Control Services Are Essential
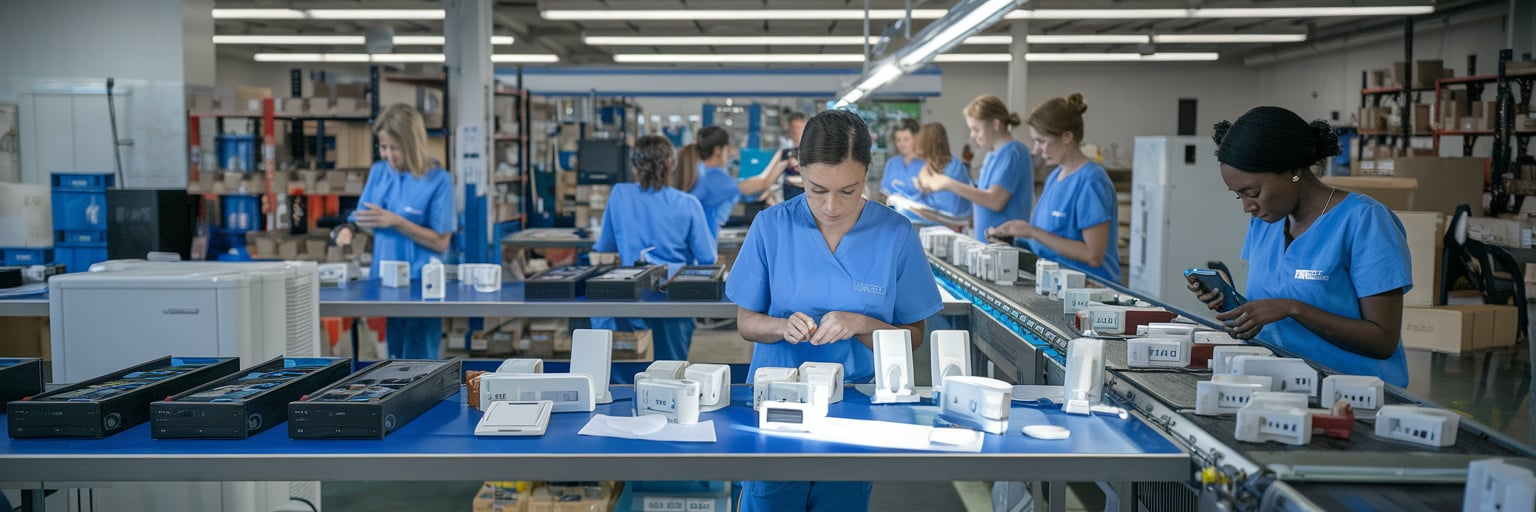
Third-party QC services offer an unbiased assessment of your products, ensuring that they meet your quality standards without any internal influence. These services are especially valuable for companies that:
Manufacture in overseas markets
When you can’t be physically present at the production site.
Lack in-house QC resources
To avoid the cost of maintaining a dedicated quality control team.
Operate in industries with stringent compliance requirements
Such as medical devices, electronics, or automotive sectors.
Key Types of Quality Control Services
When seeking third-party QC services, it’s important to understand the types of inspections and testing they can perform. Here are some of the most common:
1. Pre-Production Inspections (PPI)
Conducted before manufacturing begins, PPIs help verify that the raw materials and production processes meet your requirements. This early-stage intervention can prevent costly errors later in production.
2. During Production Inspections (DPI)
Also known as in-process inspections, DPI ensures quality consistency while the production is ongoing. Inspectors check random samples from the production line to detect and rectify issues before they escalate.
3. Pre-Shipment Inspections (PSI)
Performed after production is complete but before shipment, PSI ensures that the final products meet your specifications. This step includes visual inspections, functionality tests, and packaging checks.
4. Container Loading Inspections (CLI)
CLI verifies that the products are correctly loaded into containers, ensuring that they are packed securely and that the quantity matches the order. This minimizes damage during transit.
5. Lab Testing
For industries requiring specific certifications, such as RoHS compliance or material safety, third-party QC providers often offer laboratory testing services. These tests validate that your products meet regulatory and safety standards.
How to Choose a Third-Party QC Service Provider
When selecting a third-party QC service, it’s crucial to consider several factors to ensure you partner with a reliable and competent provider:
1. Industry Expertise
Different industries have unique quality standards and compliance requirements. Choose a QC provider with proven experience in your industry, whether it’s consumer electronics, textiles, or industrial machinery.
2. Geographic Reach
If your production spans multiple countries, look for a QC provider with a broad geographic presence. This ensures consistent quality oversight across all your manufacturing sites.
3. Range of Services
Ensure that the QC provider offers a comprehensive suite of services, including on-site inspections, lab testing, and compliance certifications. This flexibility allows you to adapt the QC process to your specific needs.
4. Accreditation and Certifications
Verify that the QC provider holds relevant certifications, such as ISO 9001 or ISO/IEC 17025 for testing and calibration laboratories. These credentials demonstrate their adherence to international quality management standards.
5. Real-Time Reporting
Timely and transparent reporting is essential for effective quality control. Look for providers that offer real-time inspection reports, complete with photos, videos, and detailed findings, so you can make informed decisions quickly.
Where to Find Third-Party QC Services
Several resources can help you identify reputable third-party QC providers:
1. Industry Directories and Networks
Professional directories like the International Organization for Standardization (ISO) database or local trade associations often list accredited QC service providers.
2. Online Platforms
Websites such as Alibaba, Global Sources, and Made-in-China frequently feature listings for QC providers alongside manufacturers. These platforms allow you to compare services and read client reviews.
3. Referrals from Industry Peers
Networking within your industry can yield valuable recommendations for trusted QC providers. Peers who have successfully used third-party QC services can provide firsthand insights into their reliability and performance.
4. Independent QC Firms
Many independent firms specialize solely in quality control services. Notable examples include:
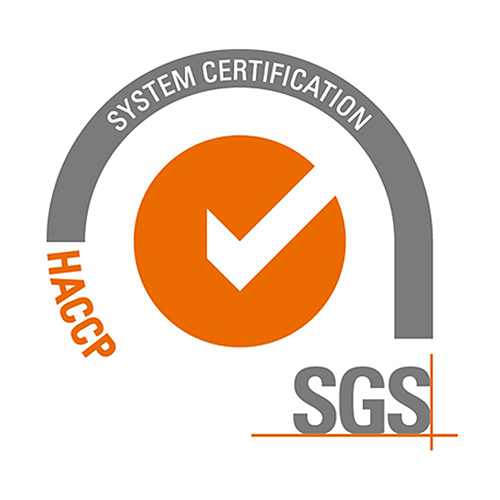
SGS
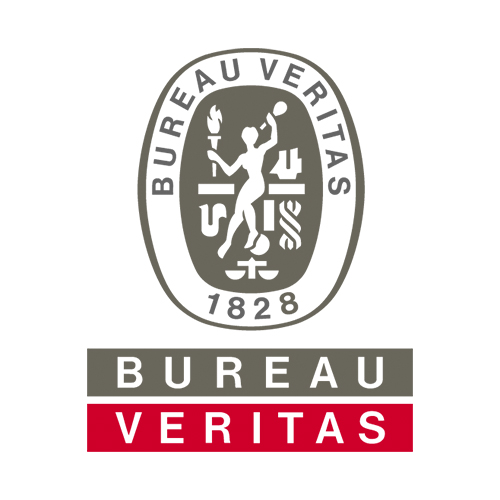
Bureau Veritas
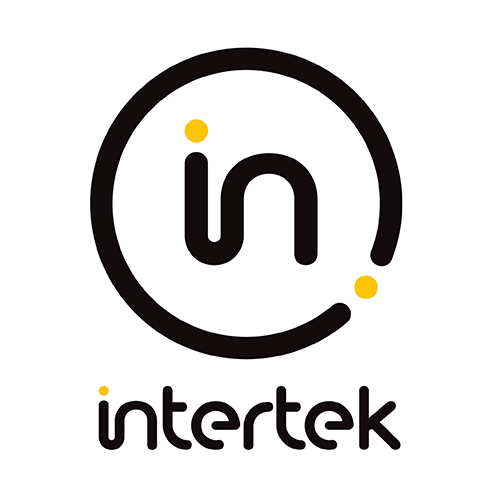
Intertek
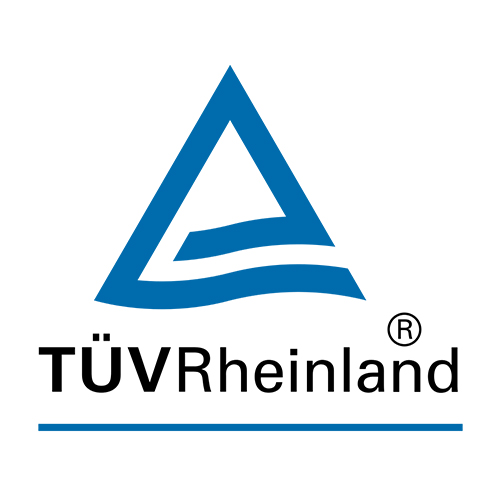
TÜV Rheinland
These companies have established reputations for delivering comprehensive QC solutions across a wide range of industries and regions.
The Benefits of Partnering with a Third-Party QC Provider
Engaging a third-party QC service provider offers numerous advantages:
· Objective Assessments: Independent inspections eliminate potential bias from internal teams.
· Cost Savings: Catching defects early reduces the financial impact of recalls or rework.
· Compliance Assurance: Ensure that your products meet all regulatory and safety standards.
· Customer Satisfaction: Delivering consistent quality builds brand trust and loyalty.
Third-party quality control services are a critical component of modern supply chain management, offering peace of mind that your products meet the highest standards. By selecting a provider with the right expertise, geographic reach, and service offerings, you can ensure consistent quality and safeguard your brand reputation.
Whether you’re a small business or a global enterprise, investing in reliable third-party QC services is a step toward operational excellence and customer satisfaction.