Sampling plays a crucial role in quality control and assurance processes across various industries. The objective of sampling is to obtain representative information about a population or a batch of products to make informed decisions. Zero Acceptance Number (ZAN) sampling plans are an intriguing approach that challenges conventional thinking by allowing no defective items to be accepted. In this article, we will delve into the concept of ZAN sampling plans, their advantages, limitations, and real-world applications.
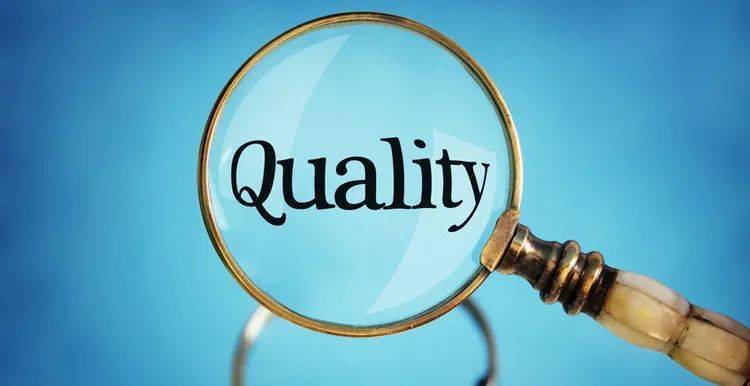
What is Zero Acceptance Number Sampling Plans?
Zero Acceptance Number (ZAN) sampling plans are a specific type of acceptance sampling plan used in quality control processes. Unlike traditional acceptance sampling plans, ZAN plans allow for no defective items to be accepted within a sample. In other words, if even a single defective item is found in the sample, the entire lot or batch is rejected.
Key features and components of ZAN sampling plans
The purpose of ZAN sampling plans is to set a high standard for quality control, ensuring that only products or lots with zero defects are accepted. This approach aims to minimize the risk of accepting defective items, which could potentially lead to customer dissatisfaction, product recalls, or safety concerns.
ZAN plans typically involve selecting a sample of items from a larger population or batch for quality inspection. The sample size and acceptance criteria are predetermined based on statistical calculations and requirements. The inspection process involves examining each item in the sample to determine if any defects are present. If no defects are found, the entire lot is accepted. However, if any defects are detected, the entire lot is rejected.
The key principle behind ZAN sampling plans is to establish a zero-defect standard and hold suppliers and manufacturers accountable for meeting this standard. By implementing ZAN plans, organizations can enhance their quality control processes, build trust with customers, and maintain a strong reputation for delivering defect-free products.
Theoretical Foundation of Zero Acceptance Number Sampling Plans
The theoretical foundation of Zero Acceptance Number (ZAN) sampling plans lies in the field of acceptance sampling theory and statistical inference. These principles provide the basis for understanding and implementing ZAN plans effectively. Let’s explore the key theoretical foundations of ZAN sampling plans:
1. Acceptance Sampling Theory:
Acceptance sampling theory deals with the statistical techniques and methodologies used to make decisions about accepting or rejecting a batch or lot based on a sample. The theory aims to strike a balance between the cost of inspection and the risk of accepting defective items. ZAN sampling plans represent a specific approach within this theory.
2. Statistical Inference:
Statistical inference plays a vital role in ZAN sampling plans. It involves using sample data to make inferences or draw conclusions about the characteristics of a larger population or batch. ZAN plans rely on statistical inference to assess the quality of a lot based on the inspection results of the sample.
3. Sampling Distributions:
Sampling distributions are fundamental to ZAN sampling plans. These distributions help determine the probabilities of different outcomes and provide insights into the characteristics of the population being sampled. Commonly used distributions in ZAN plans include the binomial distribution, hypergeometric distribution, and Poisson distribution, depending on the specific context and characteristics of the defects being inspected.
4. Type I and Type II Errors:
ZAN sampling plans involve making decisions based on the results of the sample inspection. These decisions can lead to two types of errors:
– Type I Error: This error occurs when a lot is rejected even though it meets the required quality standard. In ZAN plans, a Type I error corresponds to rejecting a lot that contains zero defects.
– Type II Error: This error occurs when a lot is accepted despite having defects. In ZAN plans, a Type II error would mean accepting a lot that contains one or more defects.
5. Statistical Power and Consumer’s Risk:
In ZAN sampling plans, statistical power and consumer’s risk are essential concepts. Statistical power refers to the probability of correctly rejecting a lot that does not meet the quality standard (avoiding a Type II error). Consumer’s risk, on the other hand, refers to the probability of incorrectly accepting a lot with defects (committing a Type II error). Balancing these two factors is critical in determining the appropriate sample size and acceptance criteria in ZAN plans.
6. Statistical Calculations and Decision Rules:
ZAN sampling plans rely on statistical calculations and decision rules to determine the sample size, acceptance criteria, and decision boundaries. These calculations are based on statistical methods such as hypothesis testing, confidence intervals, and operating characteristic curves. The objective is to establish a robust framework that minimizes the risk of accepting defective items while considering practical constraints.
By leveraging these theoretical foundations, organizations can design ZAN sampling plans that align with their quality objectives, minimize the risk of accepting defective items, and ensure a high level of product quality and customer satisfaction.
Advantages of Zero Acceptance Number Sampling Plans
- – Enhanced quality control capabilities
- – Increased confidence in the product’s quality
- – Reduced risk of accepting defective items
- – Improved customer satisfaction and brand reputation
Limitations of Zero Acceptance Number Sampling Plans
- – Increased inspection costs and time
- – Challenging implementation for large-scale production
- – Potential conflicts with suppliers and stakeholders
- – Lack of flexibility for process improvement and adjustment
Application of Zero Acceptance Number Sampling Plans in Manufacturing
Zero Acceptance Number (ZAN) sampling plans are a quality control technique used in manufacturing to ensure that the produced items meet specific quality standards. Unlike traditional sampling plans where a certain number of defects are allowed, ZAN sampling plans have a strict criterion that does not allow any defects in the sampled batch. Here are some applications of ZAN sampling plans in manufacturing:
1. Critical Components: ZAN sampling plans are commonly used for critical components that are crucial for the proper functioning of a product. These components may have high safety implications or are essential for the performance of the final product. Examples include aircraft engine parts, medical device components, or automotive safety systems.
2. Regulatory Compliance: In industries where strict regulations are in place, ZAN sampling plans can be used to ensure compliance with regulatory standards. For example, pharmaceutical manufacturing must adhere to rigorous quality standards, and ZAN plans can help in verifying that no defective or contaminated products are released to the market.
3. High-Reliability Applications: ZAN sampling plans are suitable for manufacturing processes that require high reliability and have very low tolerance for defects. Industries such as aerospace, defense, and telecommunications often employ ZAN plans to maintain high-quality standards for critical systems and equipment.
4. Low Defect Tolerance: In some manufacturing processes, even a small number of defects can result in significant consequences, such as product failures, safety hazards, or costly rework. ZAN sampling plans can be applied to minimize the risk of such defects by implementing stringent quality control measures.
5. Early Detection of Process Deviations: ZAN sampling plans can also be used as an early warning system to detect process deviations or failures. By employing ZAN plans, any deviation from the zero-defect standard triggers an investigation into the root cause, allowing manufacturers to identify and rectify the issues promptly.
6. Supplier Quality Control: ZAN sampling plans can be applied in supplier quality control programs to ensure that incoming raw materials or components from external sources meet the required quality standards. By implementing ZAN plans, manufacturers can minimize the risk of defective inputs that could affect the final product quality.
ZAN sampling plans are not suitable for all manufacturing scenarios. They are typically used in situations where the cost of defects is high, the consequences of failure are severe, or when strict regulatory requirements are in place. Additionally, implementing ZAN plans may require increased inspection efforts and closer monitoring of manufacturing processes to maintain the zero-defect standard.
When to Use Zero Acceptance Number Sampling?
Zero acceptance number sampling is a quality control technique that involves inspecting a batch or lot of products or materials and accepting or rejecting the entire lot based on the results of the inspection. It is typically used when the consequences of accepting a defective item are severe, and the cost of inspection is relatively low compared to the cost of the consequences.
Here are some situations where zero acceptance number sampling may be appropriate:
1. Safety-critical products: If the products being inspected have direct implications for safety, such as medical devices, aircraft components, or food products, a zero acceptance number sampling plan may be used. In such cases, even a single defective item could pose a significant risk to human life or well-being, so a zero-tolerance policy is implemented.
2. Expensive or irreparable items: When the cost of manufacturing a product is high, and any defect cannot be easily repaired or corrected, zero acceptance number sampling may be employed. This is often the case with complex electronic equipment, specialized machinery, or custom-made items where rectifying defects is impractical or prohibitively expensive.
3. Legal or contractual requirements: In certain industries, there are legal or contractual obligations that demand strict quality control standards. For instance, government contracts or regulatory bodies may require a zero acceptance number sampling plan to ensure compliance with specific quality standards.
4. Reputation protection: Companies that prioritize their brand image and reputation may opt for zero acceptance number sampling to maintain a consistent level of quality. Any compromise in quality could lead to customer dissatisfaction, negative reviews, and damage to the brand’s reputation.
5. Low-cost inspection: If the cost of inspecting each item in a batch or lot is relatively low compared to the consequences of accepting a defective item, zero acceptance number sampling can be an efficient quality control method. It allows for a quick decision on the acceptance or rejection of the entire lot, minimizing inspection costs.
How To Use Zero Acceptance Number Sampling?
Zero acceptance number sampling is a quality control technique that involves inspecting a batch or lot of products or materials and accepting or rejecting the entire lot based on the results of the inspection. Here are the general steps to use zero acceptance number sampling:
1. Define the inspection criteria: Determine the specific characteristics or attributes that will be inspected and the criteria that must be met for acceptance. These criteria should be clearly defined and measurable.
2. Determine the sample size: Decide on the number of items that will be randomly selected from the lot for inspection. The sample size should be statistically significant and representative of the entire batch.
3. Conduct the inspection: Inspect each item in the sample according to the defined criteria. Ensure that the inspection process is rigorous and consistent to maintain objectivity.
4. Determine the acceptance decision: If any defective items are found during the inspection, the entire lot is rejected. This means that even a single defective item results in the rejection of the entire batch. However, if no defects are found, the lot is accepted.
5. Document the results: Record the inspection results, including the number of defective items (if any) and the decision to accept or reject the lot. This documentation is essential for traceability and future reference.
6. Take appropriate action: Based on the acceptance decision, take the necessary actions. If the lot is accepted, it can proceed to the next stage or be shipped to customers. If the lot is rejected, investigate the cause of the defects, take corrective actions, and decide whether to rework or scrap the entire batch.
7. Continuous improvement: Analyze the inspection results and feedback to identify patterns, trends, or recurring issues. Use this information to improve the manufacturing or sourcing processes and prevent similar defects in the future.
It is worth mentioning that zero acceptance number sampling requires careful consideration of the risks associated with defects and the cost of inspection. It is not suitable for all situations, and alternative sampling plans, such as statistical sampling with an acceptable quality level (AQL), may be more appropriate in some cases.
Zero Acceptance Number (ZAN) sampling plans provide a unique approach to quality control, offering increased confidence in product quality and customer satisfaction. While they come with certain limitations, their advantages and successful implementation examples across various industries highlight their potential. As statistical techniques and calculation methods evolve, and with the integration of emerging technologies, ZAN plans are likely to find broader application in the future. By understanding the foundations, benefits, and challenges of ZAN sampling plans, organizations can make informed decisions to improve their quality control processes and deliver superior products and services.