If we can establish correct concepts and implement effective quality management plans, we can prevent the occurrence of defective products. What is zero defect management and how to implement it?
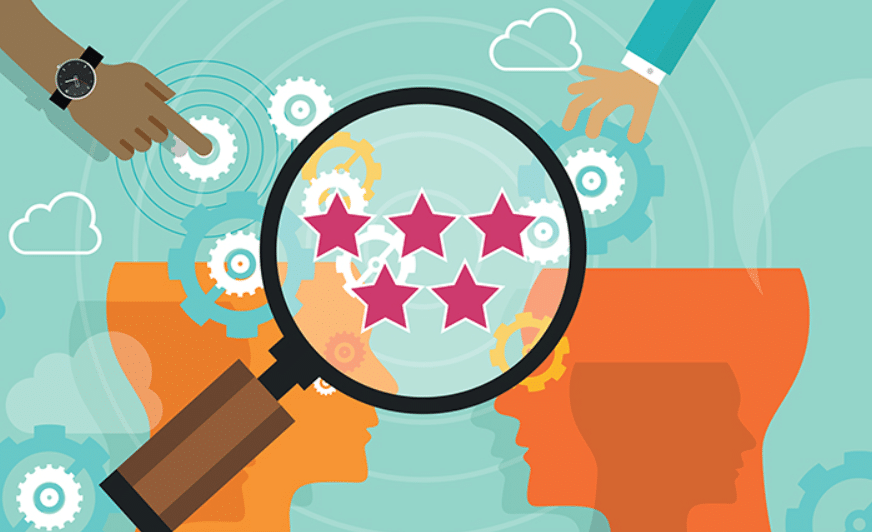
What is Zero Defect Management?
Zero defect is called ZD for short. It is also called defect prevention. The idea of zero defect management advocates that enterprises should give play to the subjective initiative of people to conduct business management. Producers and workers should strive to make their products and businesses free of defects and strive for the goal of high quality standards. It is a quality management activity that is guided by abandoning the theory that “shortcomings are inevitable”, establishing the philosophy concept of “no defects”, requiring all staff to “work correctly from the beginning”, and aiming at completely eliminating work shortcomings. Zero defect does not mean that there is absolutely no defect, or the defect must be equal to zero, but it means that “defect is equal to zero as the ultimate goal, and everyone should strive to be faultless within their own work responsibilities.” It requires production workers to do their work accurately and conscientiously from the beginning, and make reasonable arrangements in terms of product quality, cost and consumption, delivery date, etc, Instead of relying on post test to correct. Zero defect places special emphasis on prevention system control and process control. It requires doing things right the first time to make the product meet the requirements of the customer’s commitment. The zero defect campaign can improve the sense of responsibility of all staff for product quality and business quality, thus ensuring product quality and work quality.
Basic Principles of Zero Defect Management
The basic connotation and principle of zero defect management can be summarized as follows: based on the purpose and goal, through the whole process and all-round management of all aspects of the operation, ensure that the defects of all elements at all levels of all aspects tend to zero. The specific requirements are:
1) All phases should not transmit defective decisions, information, materials, technologies or parts to the next link, and enterprises shall not provide defective products and services to the market and consumers.
2) Management systems and specifications must be established at each level of each link, management shall be implemented according to the specified procedures, responsibilities shall be implemented in place, and loopholes out of control are not allowed.
3) Each link and each level must have preventive and in-process corrective measures for product or work errors to ensure that errors do not continue and are eliminated in advance.
4) In the management of all elements, we should focus on the management of people, improve the incentive mechanism and constraint mechanism, give full play to the subjective initiative of each employee, so that they are not only the managed, but also the managers, and guarantee the zero defect of products, work and enterprise operation with zero defect subject behavior.
5) The entire enterprise management system is adjusted in time according to market requirements and enterprise development changes. Perfect, realize dynamic balance, and ensure that the management system has the best adaptability and adaptability to the market and enterprise development.
Implementation Steps of Zero Defect Management
To implement the philosophy of zero defect management in the enterprise, so that every employee can grasp its essence, establish the determination of not making mistakes, and actively put forward suggestions to the superior, it must be prepared and planned to implement. The following steps can be taken to implement zero defect management:
1) Establish an organization to promote zero defect management. The implementation of the event requires the guarantee of the organization. Through the establishment of the organization, we can mobilize and organize all employees to actively invest in zero defect management, and improve their consciousness of participating in management; It is also possible to conduct statistical analysis on each person’s reasonable suggestions, and constantly exchange experience. The top management of the company should attend in person, show their determination and set an example; We should appoint corresponding leaders and establish corresponding systems; Educate and train employees.
2) Determine the goal of zero defect management. Determine the specific requirements to be met by the zero defect team (or individual) in a certain period, including determining the target project, evaluation criteria and target value. In the process of implementation, various forms shall be adopted to timely publish the progress of the team in achieving the goals and pay attention to the psychological impact.
3) Conduct performance evaluation. Whether the objectives determined by the group are achieved shall be evaluated by the group itself, and the responsibilities and authorities of the group shall be clarified.
4) Establish corresponding proposal system. The direct staff can point out the cause of the error to the team leader, make suggestions, and attach relevant improvement plans for the error causes not attributable to their own subjective factors, such as equipment, tools, drawings and other problems. The team leader shall study and handle with the proposer.
5) Establish a recognition system. Flawless management is not to reprimand the wrong person, but to commend the flawless person; It is not to point out how many shortcomings people have, but to tell people to strive for the goal without defects. This strengthens the confidence and sense of responsibility of the staff to eliminate their shortcomings.