Processes
- Polymer Processing
- Injection Molding Insert Molding Blow Molding Over Molding Metal Injection Molding Thermoforming
- Metal Casting
- Die Casting Castings & Forgings Wax Casting Lost Wax Casting Grey Iron Castings Centrifugal Casting Investment Casting Permanent Mold Sand Casting Shell Mold Casting Aluminum Investment Casting Brass Investment Casting Steel Investment Castings Titanium Investment Casting
- Machining
- Milling Turning EDM machining CNC Engraving Hole-making Tap Size Chart Drill Size Chart 5 axis machining Micro Machining CNC Cutting Metal Processes Ceramic Manufacturing Swiss Precision Machining
Materials
3D printing, also known as additive manufacturing, is the process of creating a three-dimensional item from a CAD model or digital 3D model. The phrase 3D printing refers to some methods in which material is deposited, connected, or solidified under computer control to make a three-dimensional item, with the material being added together (such as polymers, liquids, or powder grains being fused), often layer by layer.
The Massachusetts Institute of Technology invented 3D printing technology, which was licensed to various firms. The procedure is similar to Selective Laser Sintering (SLS), except that instead of a laser, an ink-jet printing head drops a liquid adhesive that bonds the material. The material alternatives, which include metal or ceramic powders, are rather restricted but relatively affordable in comparison to other additive methods. Fast build rates, generally 2-4 layers per minute, are a benefit of 3D printing. However, precision, surface smoothness, and component strength are not as excellent as in other additive methods. Typically, 3D printing is utilized for quick prototyping conceptual models.
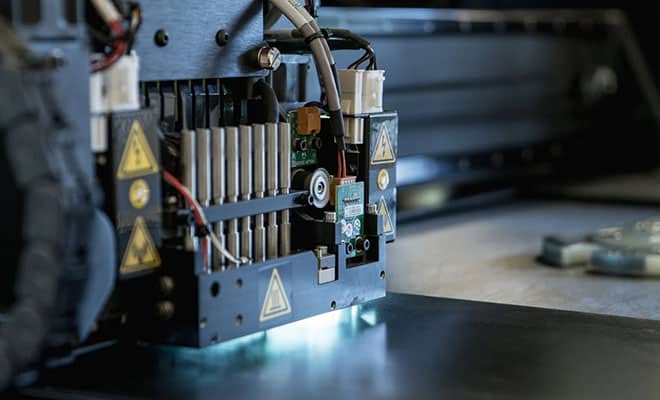
The 3D Rapid Prototyping Process
The 3D printing process starts with a piston raising the power supply and a leveling roller dispersing a small coating of powder to the top of the build chamber. The liquid glue is then applied to specific areas of the powder bed by a multi-channel ink-jet print head. The adhesive bonds these powder areas together, forming one layer of the component. During the construction, the leftover free-standing powder acts as a support for the portion. After completing a layer, the build platform is lowered, a fresh layer of powder is added, leveled, and the printing process is repeated. After finishing the portion, the loose supporting powder may be brushed away and the part removed. To increase strength and surface quality, 3D printed objects are generally penetrated with a sealant. In the construction of a three-dimensional item using additive manufacturing, a range of procedures, equipment, and materials are employed. Because 3D printing is also known as additive manufacturing, the many 3D printing processes available tend to be additive with a few significant variances in the technology and materials utilized in this process. Melt extrusion, light polymerization, continuous liquid interface creation, and sintering are some of the physical changes employed in 3D printing.
There are several 3D printing techniques, which may be classified into seven categories: Vat photopolymerization, Inkjet Technology, Binder jetting, powder bed fusion, material extrusion, Directed energy deposition, and sheet lamination are all terms used to describe vat photopolymerization. Each technique and piece of equipment has advantages and disadvantages. These typically include elements such as speed, cost, feedstock variety, geometrical restrictions, and tolerances, as well as mechanical and aesthetic attributes of the products such as strength, texture, and color. The diversity of procedures and equipment enables a wide range of applications by both amateurs and experts. Some are more suited for industrial usage, while others make 3D printing accessible to the typical customer. Some printers can create skyscrapers, while others focus on micro and nanoscale-sized structures. In general, many various technologies may be used to physically manufacture the specified structures.
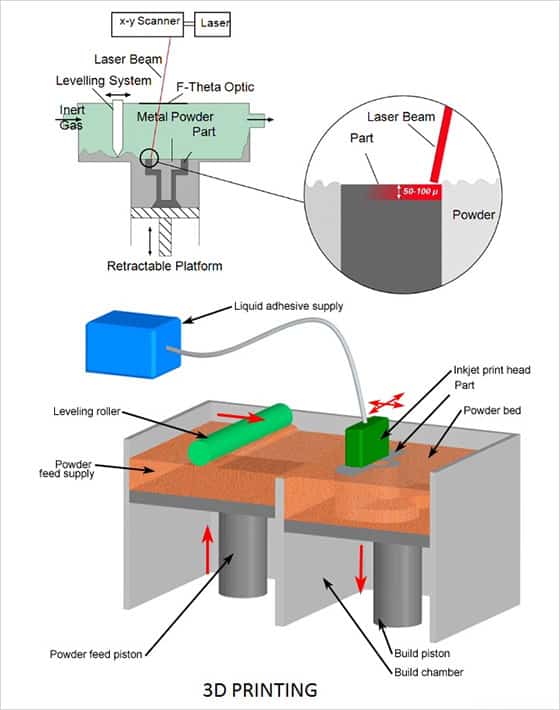
Applications
Manufacturing Applications: Cloud-based additive manufacturing, Mass customization, Rapid manufacturing, Rapid prototyping, Research, Food, Agile tooling
Medical Applications: Bio-printing, Medical devices, Pharmaceutical Formulations, Industrial applications, Apparel, Industrial art and jewelry, Automotive industry, Construction, home development, Firearms, Computers and robots, Soft sensors and actuators, Space
Sociocultural Applications: Art and jewelry, 3D selfies, Communication, Domestic use, Cultural heritage, Environmental use, Education and research, Specialty materials
3D Printing Capabilities | |
---|---|
Abbreviation | 3DP |
Min Feature Size | 0.008 in. |
Tolerance | 0.004 in. |
Min Layer Thickness | 0.002 in. |
Max Part Size | 59.00 x 29.50 x 27.60 in. |
Surface finish | Rough |
Material type | Powder |
Build speed | Very Fast |
Materials | Non-Ferrous/Ferrous metals(Bronze/Stainless Steel, etc); Elastomers; Composites; Ceramics |