Processes
- Polymer Processing
- Injection Molding Insert Molding Blow Molding Over Molding Metal Injection Molding Thermoforming
- Metal Casting
- Die Casting Castings & Forgings Wax Casting Lost Wax Casting Grey Iron Castings Centrifugal Casting Investment Casting Permanent Mold Sand Casting Shell Mold Casting Aluminum Investment Casting Brass Investment Casting Steel Investment Castings Titanium Investment Casting
- Machining
- Milling Turning EDM machining CNC Engraving Hole-making Tap Size Chart Drill Size Chart 5 axis machining Micro Machining CNC Cutting Metal Processes Ceramic Manufacturing Swiss Precision Machining
Materials
What is Hole Making?
Hole making is a kind of special machining operation for cutting holes into workpieces. Hole making operations can be performed on a wide range of machines including CNC milling machines or lathes, through cutting away the unwanted materials. Common specialized tools for hole making are drill presses and tapping machines. Drilling, roaming and boring are all typical operations for getting holes with the desired sizes and precision. Drilling is often the starting point for other operations. Hole making is often performed among many other operations in the machining process of a part, but it can also be used as a secondary processing method for castings or forgings.
Types of Hole Making Operations
- Drilling: a machining process for making cylindrical holes with a drill bit. The drill enters the workpiece axially and cuts out a blind hole or through hole with the same diameter as the bit. In drilling process, a drill is a multipoint tool, usually with a sharp tip. A twist drill is the most commonly used drilling tool.
- Reaming: the process of finishing holes or slightly removing materials from the hole with a reamer that has multiple cutting edges. In reaming process, the reamer enters the workpiece axially and expands the existing hole to the tool diameter. Reamer is a multi-point tool with many flutes, which can be straight or spiral. Reaming removes the least amount of material, usually after drilling, to achieve a more accurate diameter and smoother surface finish.
- Boring: the process of enlarging the drilled hole using a boring bar. In the boring process, the boring bar enters the workpiece axially and cuts along the inner surface of the existing hole to enlarge the diameter or obtain more accurate dimensions. A boring cutter is a kind of single-point cutting tool, which can be set to the required cutting diameter by using an adjustable boring head.
- Tapping: the process of cutting a thread inside a hole so that a screw or bolt can be threaded into the hole, it can also be used to make a thread on nuts. Tapping operation can be done on lathe machine. Different taps are available to match almost any screw type, based on the metric and standard measurements.
- Counterboring: also known as counter boring, the operation of enlarging an existing hole to be concentric with the original hole and the bottom to be square. This is done to fit the bolt head, stud, and pin. The cutting edge of a counter-bore (a tool for counter boring) can be straight or helical.
- Countersinking: the process of forming a V-shaped edge near the surface of the hole. It is usually used to deburr drilled or tapped holes, or to make the head of a countersunk screw flush or below the surface. In CNC milling, chamfering end mills are usually used to make countersinks.
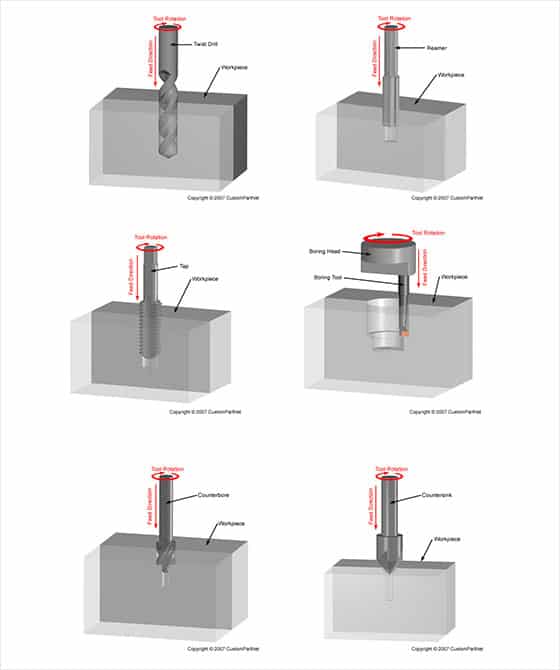
Features of Machined Holes
A machined hole can be characterized by some different features or parameters that can determine the required hole making operations and tools.
- Diameter: holes can be machine to a wide range of diameters, which depending on the size of the used tool, the drill bit and taps are available in standard sizes, a custom tool can also be made to process a non-standard diameter, but using standard tools is more cost-effective and convenient.
- Depth: a hole can extend to a certain point inside the workpiece, which is called a blind hole, or it may completely extend out of the workpiece, which is called a through the hole. Blind holes may have a flat bottom but usually end with a dot due to the tip of the tool. When specifying the depth of a hole, you can refer to the depth to the point. The total depth of the hole is limited by the tool length.
- Tolerance: the cutting precision will be affected by many factors, including the sharpness of the tool, any vibration of the tool, or the accumulation of cutting chips. The specified tolerance of the hole will determine the hole making method selection, only some of them can provide holes with tight tolerance.
- Thread: sometimes a threaded hole is required to accommodate a threaded fastener, usually specified by its outside diameter and pitch. Pitch is the measurement of thread spacing, it can be indicated as per metric standard or English standard.
- Recessed top: the top of the hole is recessed into the workpiece. This is usually to fit the head of the fastener so that it is flush with the surface of the workpiece. Two types of recessed holes are counterbore and countersink.
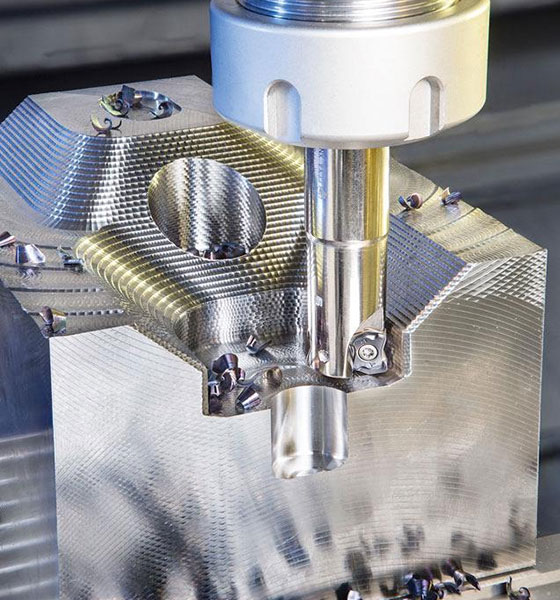