Processes
- Polymer Processing
- Injection Molding Insert Molding Blow Molding Over Molding Metal Injection Molding Thermoforming
- Metal Casting
- Die Casting Castings & Forgings Wax Casting Lost Wax Casting Grey Iron Castings Centrifugal Casting Investment Casting Permanent Mold Sand Casting Shell Mold Casting Aluminum Investment Casting Brass Investment Casting Steel Investment Castings Titanium Investment Casting
- Machining
- Milling Turning EDM machining CNC Engraving Hole-making Tap Size Chart Drill Size Chart 5 axis machining Micro Machining CNC Cutting Metal Processes Ceramic Manufacturing Swiss Precision Machining
Materials
What Is Sheet Metal Fabrication
Sheet metal fabrication is not only a pivotal technology that sheet metal technicians need to grasp, but also an important process of sheet metal product forming. Sheet metal fabrication includes traditional cutting, punching, bending, welding and other methods to form different shapes. It includes various cold stamping die structures and process parameters, various equipment working principles and operation methods, as well as new stamping technology and new process.
Sheet metal parts can be processed by stamping, bending, stretching and other means. A general definition is parts with constant thickness in the processing process, corresponding to casting parts, forging parts, machining parts, etc. The size of sheet metal parts can range from a small washer or bracket, to midsize enclosures for home appliances, to large airplane wings. These parts are found in a variety of industries, such as aircraft, automotive, construction, consumer products, HVAC, and furniture.
Materials Used In Sheet Metal Fabrication
The materials commonly used in sheet metal processing include cold rolled plate (SPCC), hot rolled plate (SHCC), galvanized plate (SECC, SGCC), copper (Cu), brass, red copper, beryllium copper, aluminum plate (6061, 5052, 1010, 1060, 6063, hard aluminum, etc.), stainless steel (mirror, wire drawing surface, fog surface). According to the different functions of products, different materials are selected, Generally, the use and cost of the product shall be considered.
- Cold rolled sheet SPCC mainly uses electroplating and paint baking parts, with low cost, easy forming and material thickness ≤ 3.2mm.
- Hot rolled plate SHCC, material t ≥ 3.0mm, is also electroplated and painted parts, with low cost but difficult to form, mainly flat parts.
- Galvanized sheet SECC, SGCC. SECC electrolytic plate is divided into n material and P material. N material is mainly not subject to surface treatment and has high cost. P material is used for spraying parts.
- Copper; It mainly uses conductive materials, and its surface treatment is nickel plating, chromium plating, or no treatment, with high cost.
- Aluminum plate; Generally, surface chromate (j11-a) and oxidation (conductive oxidation and chemical oxidation) are used, with high cost, including silver plating and nickel plating.
- Aluminum profile; Materials with complex cross-section structure are widely used in various plug-in boxes. The surface treatment is the same as that of aluminum plate.
- Stainless steel; It is mainly used without any surface treatment and has high cost.
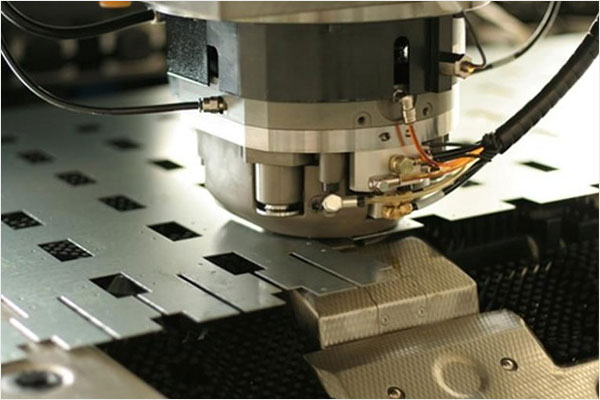
Sheet Metal Fabrication Processes
Sheet metal fabrication processes can mostly be placed into two categories – forming and cutting. Forming processes are those in which the applied force causes the material to plastically deform, but not to fail. Such processes are able to bend or stretch the sheet into the desired shape. Cutting processes are those in which the applied force causes the material to fail and separate, allowing the material to be cut or removed. Most cutting processes are performed by applying a great enough shearing force to separate the material, and are therefore sometimes referred to as shearing processes. Other cutting processes remove material by using heat or abrasion, instead of shearing forces.
Forming
- Bending
- Roll forming
- Spinning
- Deep Drawing
- Stretch forming
Cutting with shear
- Shearing
- Blanking
- Punching
Cutting without shear
- Laser beam cutting
- Plasma cutting
- Water jet cutting
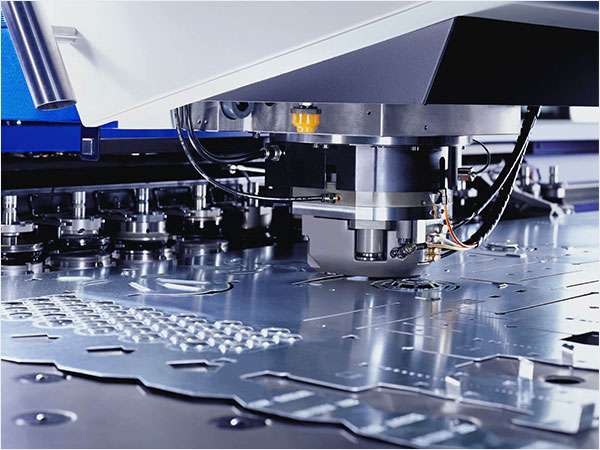
Pros & Cons Of Sheet Metal Fabrication
Advantages
- Can form complex shapes
- Many material options
- High production rate
- Low labor cost
- Short lead time possible
Disadvantages
- Limited to constant part thickness
- Part may require several operations and machines
- Large amount of scrap
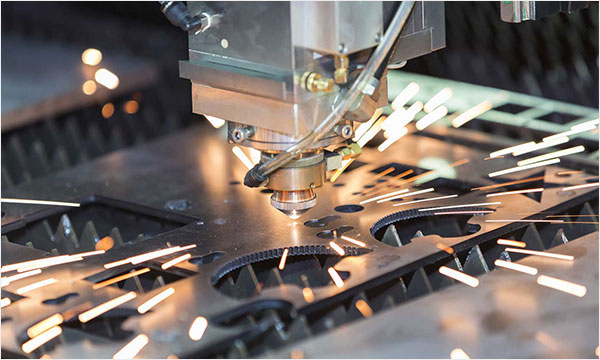
Applications Of Sheet Metal Fabrication
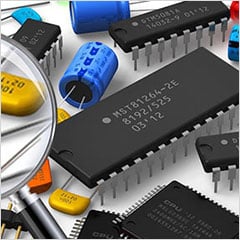
Electronics
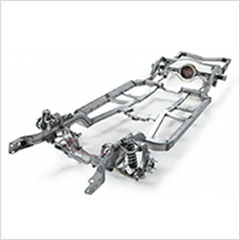
Chassis Construction
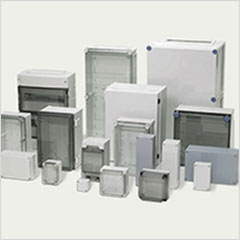
Enclosers and Housings
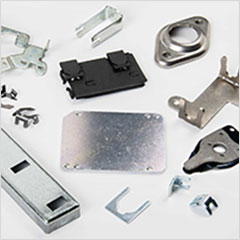
Brackets and Small Components
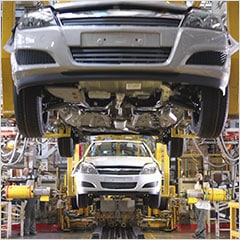
Automotive
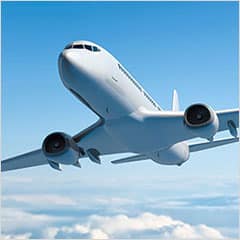
Aerospace
Sheet Metal Fabrication Tools
- CAD design software
- Prototyping technology
- Laser cutters
- Laser / punch combination machinery
- CNC punch machinery
- Folding machinery, such as manual press brakes, automated panel benders and automated robotic folders
- Precision turned parts machinery
- CNC machine tools
- Robotic welders
- Powder coating plant
- CMM technology