Processes
- Polymer Processing
- Injection Molding Insert Molding Blow Molding Over Molding Metal Injection Molding Thermoforming
- Metal Casting
- Die Casting Castings & Forgings Wax Casting Lost Wax Casting Grey Iron Castings Centrifugal Casting Investment Casting Permanent Mold Sand Casting Shell Mold Casting Aluminum Investment Casting Brass Investment Casting Steel Investment Castings Titanium Investment Casting
- Machining
- Milling Turning EDM machining CNC Engraving Hole-making Tap Size Chart Drill Size Chart 5 axis machining Micro Machining CNC Cutting Metal Processes Ceramic Manufacturing Swiss Precision Machining
Materials
Sheet Metal Cutting
During this sheet metal cutting process, the pieces that have a certain shape and their defined dimensions are separated. It is traditionally done around drilling and milling machines in other processes executed by machines with the use of various cutting tools. The parts are produced by detaching the metal in the form of small chips, in this way techniques such as laser cutting and others that can vary depending on the need are achieved.
This article describes the different sheet metal cutting processes without shearing. Its operating principle, advantages and disadvantages of each one and their respective fields of application are presented.
Laser Beam Cutting
Among all the options that exist within precision machining, one of the youngest metal cutting process is laser beam cutting.
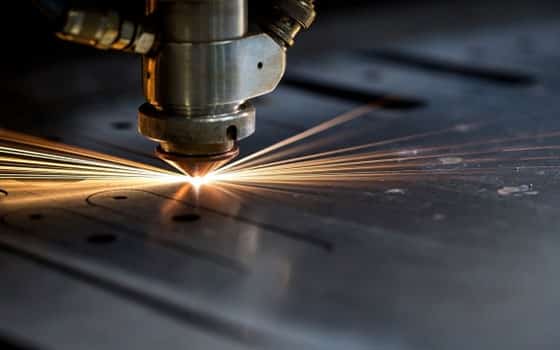
What is Laser Cutting & How Does It Work?
Laser processing mainly refers to the use of special machines to cut and drill thin plate materials (iron plate, stainless steel plate, aluminum plate, etc.).Using the light energy of the laser, it uses a lens to focus on a point and irradiate it directly, while using an auxiliary gas to purge the molten metal to cut the metal, etc.
It is not a machine tool that cuts like cutting or turning, but a machine tool that processes without direct contact with the material. Since the material is thin material such as sheet metal, steel plate, and stainless steel, it is classified as a sheet metal cutting machine.
Laser Cutting Types
Some types of lasers that are most talked about industrially are:
CO 2 laser cutting: Carbon Dioxide sealed within the laser is “pumped” (activated by heating) by an electrical current that creates the flow of photons. Laser processing machines that use this CO2 laser beam are the most popular, and generally used for cutting, drilling, welding, and engraving.
Neodymium doped yttrium-aluminum garnet (Nd-YAG) laser cutting: YAG is pumped using a lamp or diode to emit the flow of photons. YAG laser beam cutting is commonly used for cutting, welding and engraving metals such as polyethylene, polycarbonate, iron, aluminum, nickel, and stainless steel.drilling, welding, and engraving.
Fiber laser cutting: uses semiconductor diodes as the pump mechanism and an optical fiber doped with a rare earth element as a laser medium. Fiber lasers are suitable for welding difficult-to-weld materials such as copper and aluminum, and since they can be struck finely, heat is applied to pinpoints to melt them.
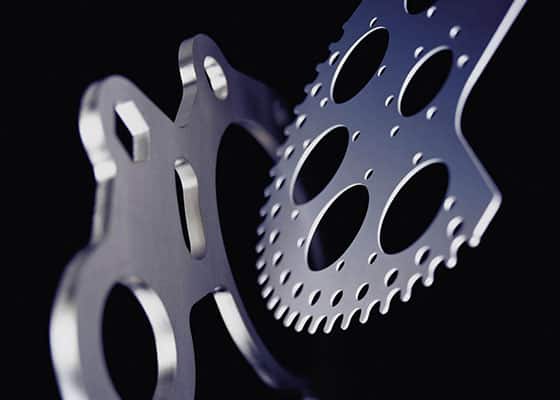
Laser Cutting Advantages & Disadvantages
Among the advantages of the laser cutting process we find the following:
- Faster than high definition plasma
- Cuts profiles in complex shape
- High precision and quality of cut pieces (especially in thicknesses small and medium)
- Reduced kerf
- Very reduced Thermally Affected Area
- Variety of materials to cut
Some drawbacks of this process are:
- ● It cannot cut reflective materials (Al, Cu, etc.)
- Reduced speed for thicknesses <3 mm
- High initial investment (compared to oxyfuel, plasma or water)
- High investment / High cost of consumables (nozzles, electrodes)
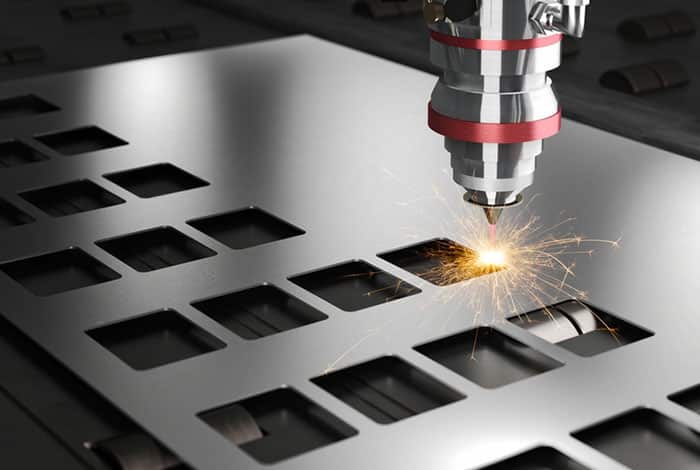
Water Jet Cutting
Probably one of the most amazing cutting procedures out there. And it is due to its simplicity, but its extreme power.Water Jet Cutting is already a common resource when machining parts, simple and at the same time very complex. It is a very versatile tool whose application can be extended to practically all jobs in the industry.
What Is Water Jet Cutting & How Does It Work?
Water jet cutting is a process of a mechanical nature by means of which it is possible to cut a material, making a jet of water impact on it at high speed that produces the desired finish. Cut processing by water jet (WJ) is to pressurize water to a maximum of 600MPa (about 6,000 atm), inject it from a small diameter nozzle (Φ0.1mm), and use the energy of high-speed, high-density ultra-high pressure water. , It is a method of cutting an object.The water pressurized by the ultra-high pressure water generation pump reaches about 3 times the speed of sound, producing a destructive water jet (WJ).
It has a wide range of uses, and in familiar areas, it is used for cutting automobile roofing materials, dashboards, and bumpers. Cutting and dismantling of concrete structures. It is used for cutting the airframe of aircraft using new materials.
Water Jet Cutting Advantages & Disadvantages
However, this process has the following advantages:
- A thermally affected zone does not originate
- It can cut any material with a wide range of thicknesses
- Does not require secondary operations
- Reduced kerf (0.5 – 1 mm)
- Small cutting force (1.4 – 2.3 kg)
- Clean process, no gases
- You can make holes to start cutting
- Safe process (low water compressibility)
- Cuts highly detailed shapes and geometries
Finally, as other drawbacks of this process, we find:
- Slower than flame cutting or plasma
- High abrasive cost (0.23 kg / min to 1 kg / min
- Noise
- High initial investment (greater than oxyfuel or plasma)
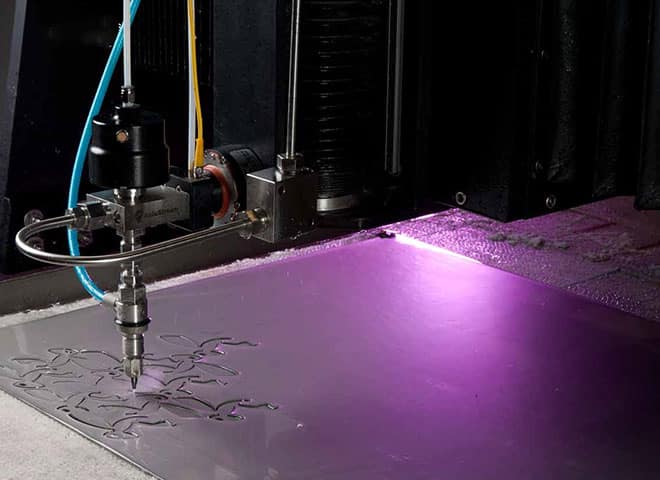
Plasma Cutting
The plasma cutting process was developed in the fifties of the last century. It was initially planned for cutting conductive metals, primarily stainless steel and aluminum. Today, plasma cutting is the fastest growing sheet metal cutting system in the industry, in service shops and in general in any place where metal cutting is required, thanks to the speed and precision of the cut.
What Is Plasma Cutting & How Does It Work?
In simpler terms, plasma cutting is a process that uses a high-speed jet of ionized gas that is sent from a constriction orifice. The high velocity of the ionized gas, which is plasma, conducts electricity from the plasma torch to the workpiece. The plasma heats the workpiece, melting the material. The high velocity flow of the ionized gas mechanically blows the molten metal, breaking up the material.
Plasma cutting is a process that uses a nozzle, with an orifice for the circulation of ionized gas at high temperatures, in such a way that a beam is obtained that can be used to cut sections of metals such as carbon steel, steel stainless, aluminum and other electrically conductive metals. Using this technique, the plasma arc melts the metal, and the gas removes the molten material.
Plasma cutting is an excellent tool to use on conductive materials (such as brass, copper, aluminum, or steel), which explains why it is often used in factories, welding shops, auto repair, restoration, industrial construction, and operations. demolition.
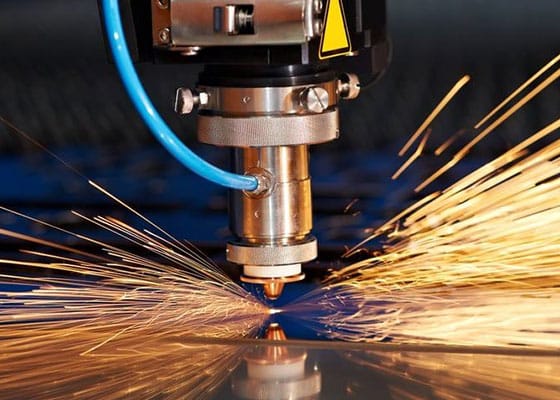
Plasma Cutting Advantages & Disadvantages
The many advantages of plasma cutting:
- It can be used on a wide range of materials, such as stainless steel or aluminum.
- Reduced cost of consumables (air).
- Low demands on the quality of materials and the work environment.
- Cutting speeds higher than laser on medium and thick plates.
- Cutting speeds higher than oxyfuel on thin and medium plates.
However, plasma cutting has some drawbacks:
- Non-conductive materials, such as wood or plastic, cannot be cut using this system
- Limited to the thickness of the plates on which it is worked
- Cannot exceed 160 mm for dry cutting and 120 mm for water cutting
- Electrode and the nozzle of the cutting device must be replaced frequently
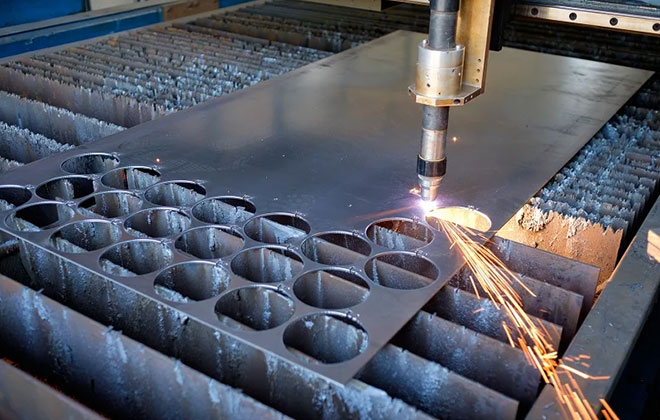