Processes
- Polymer Processing
- Injection Molding Insert Molding Blow Molding Over Molding Metal Injection Molding Thermoforming
- Metal Casting
- Die Casting Castings & Forgings Wax Casting Lost Wax Casting Grey Iron Castings Centrifugal Casting Investment Casting Permanent Mold Sand Casting Shell Mold Casting Aluminum Investment Casting Brass Investment Casting Steel Investment Castings Titanium Investment Casting
- Machining
- Milling Turning EDM machining CNC Engraving Hole-making Tap Size Chart Drill Size Chart 5 axis machining Micro Machining CNC Cutting Metal Processes Ceramic Manufacturing Swiss Precision Machining
Materials
The Definition of Laminated Object Manufacturing (LOM)
In 1991, the first industrial Laminated Object Manufacturing (LOM) machine was launched. LOM was created by Helisys of Torrance, CA. The system’s core elements include a feed mechanism that moves a sheet over a production platform, a heated roller that provides strength to attach the sheet to the layer below, and a laser that cuts the shape of the part in each sheet layer. Layers of adhesive-coated sheet material are stacked, bonded, and sliced on top of one another to form parts. The part’s outline is carved into each layer using a laser. Following the completion of each cut, the platform is lowered by a depth equal to the sheet thickness,generally 0.002-0.020 inches. and another sheet is placed on top of the previously deposited layers. After that, the platform raises gently and the heated roller provides force to attach the new layer. The outline is cut using a laser, and the operation is repeated until the component is finished. After a layer is sliced, the excess material is left in place to facilitate the component during assembly.
The Advantages Of Using LOM As The Additive Fabrication
Small-batch customization is more cost-effective than standard mass-production processes. Paper models have wood-like features and may be modified and polished as such. Using direct manufacture from a 3D CAD model eliminates the need for tools and molds, as well as the expense of conversion. Although the dimensional precision is somewhat lower than that of stereolithography and selective laser sintering, no milling step is required. The design is in the form of a digital file, making it easy to share, modify, and customize components and products. Because no chemical reaction is required, very big pieces may be produced. In addition, because of the process’s additivity, it is feasible to conserve resources and utilize waste resources.
Laminated Object Manufacturing Capabilities | |
---|---|
Abbreviation | LOM |
Min Layer Thickness | 0.002 in. |
Tolerance | 0.004 in. |
Min Feature Size | 0.008 in. |
Max Part Size | 32.00 x 22.00 x 20.00 in. |
Build Speed | Fast |
Material Type | Solid |
Surface Finish | Rough |
Materials | Paper, Plastic, Metal |
Applications | Architectural Models, Education & Design, Customized Objects For Personal/Industrial Use, etc. |
The Process Of Laminated object manufacturing
Laminated object manufacture (LOM) is a fast prototyping technique that involves building a component progressively from layers of paper. The precision and accuracy of the LOM process, as well as the dimensional stability of Laminated object manufacturing components, are studied in today’s researches. It was discovered that this technique had both consistent and variable sources of inaccuracy in the component dimensions. The highest dimensional inaccuracy was normal to the plane of the paper, which was increased by moisture absorption and subsequent swelling. The critical process parameters were discovered and improved to provide adequate bonding and cutting precision.
The preceding procedures are how the LOM process carries out:
- A heated roller was used to attach the sheet to a substrate;
- The targeted prototype’s dimensions are traced using a laser;
- Non-part area is cross-hatched using a laser to enable trash removal;
- The platform with the finished layer slides down and out of the way;
- A new sheet of material is rolled into place;
- The platform lowers into a new position in preparation for the following layer;
- The procedure is continued until a complete model or prototype is ready.
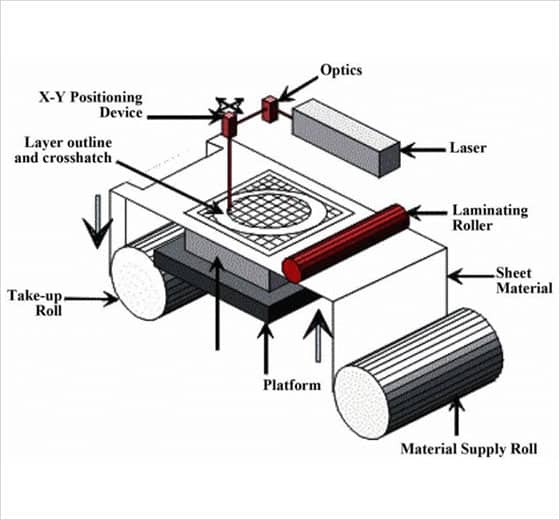