Processes
- Polymer Processing
- Injection Molding Insert Molding Blow Molding Over Molding Metal Injection Molding Thermoforming
- Metal Casting
- Die Casting Castings & Forgings Wax Casting Lost Wax Casting Grey Iron Castings Centrifugal Casting Investment Casting Permanent Mold Sand Casting Shell Mold Casting Aluminum Investment Casting Brass Investment Casting Steel Investment Castings Titanium Investment Casting
- Machining
- Milling Turning EDM machining CNC Engraving Hole-making Tap Size Chart Drill Size Chart 5 axis machining Micro Machining CNC Cutting Metal Processes Ceramic Manufacturing Swiss Precision Machining
Materials
What Is Lost Wax Casting
Lost-wax casting, also known as cire Perdue in France, cera perduta in Latin. It is a process of making simple to complex objects from various metals (such as gold, silver, brass or bronze) by casting original models or patterns. It is one of the oldest known metal-forming technologies, but it is still widely used in the production of jewelry, dentistry, and art. Its industrial form, investment casting, is a common method for manufacturing precision metal parts in engineering and manufacturing.
The History Of Lost Wax Casting
Lost wax casting technology is developed from ancient casting technology. Lost wax casting has existed for over very many years. The earliest documented known instances of this procedure are thought to go back to 3700 BC after tests with carbon-14 dating. They were found in the Cave of the Treasure crowd in southern Isra. The basic principle of modern lost wax casting technology is the same, but it is more complex and precise. This is mainly reflected in the more strict requirements for the accuracy of wax mold position.
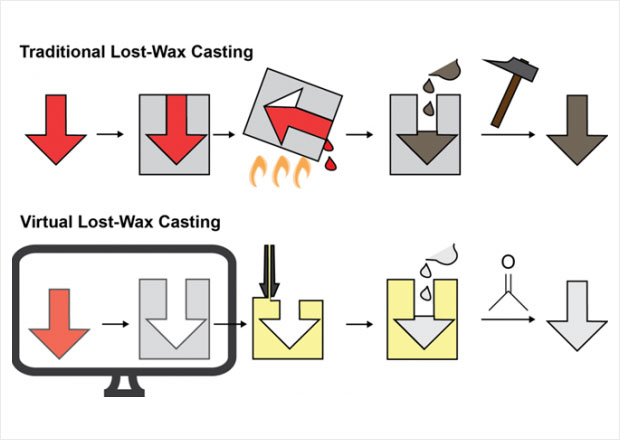
The Process Of Lost Wax Casting
The wax is made into the mold pattern to be made, and then the high-temperature resistant fine mud is poured onto the wax surface, and fine sand is sprinkled on the mud surface many times to form a complete mold shell. After drying, the wax is heated to melt out and form a mold cavity for casting copper liquid (i.e. the solution of red copper plus lead, zinc, tin and other metal elements). After casting, after shelling, polishing and aging, an exquisite antique bronze ware will be displayed in front of you.
The Material Are Used In Lost Wax Casting
Casting is a flexible investment technique, thus a variety of materials may be utilized for the production of high-quality components, light or robust, common or unusual.
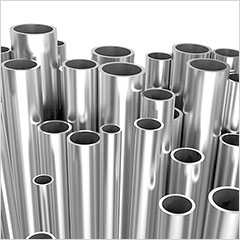
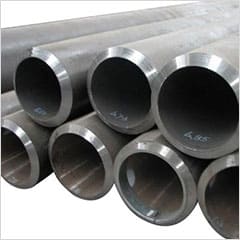
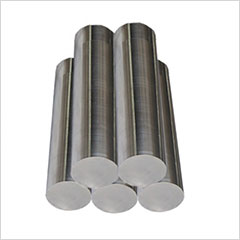
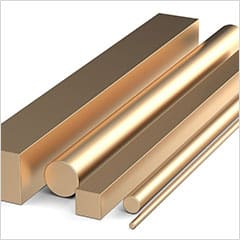
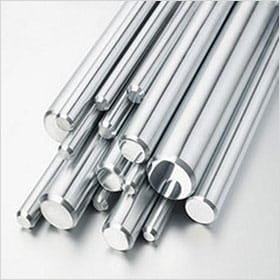
Lost Wax Casting Advantages:
- The technique is particularly advantageous for high-melting alloys and for metals that are difficult to machine.
- It is best suited for the production of tiny castings with complex forms.
- Maintains a very close ± 0.05 mm tolerance.
- The surfaces are extremely smooth.
- Most machining processes are eliminated.
- It applies to all metals and alloys with low to high melting points.
Lost Wax Casting Disadvantages:
- Investment casting includes several complicated processes which make the process more costly in comparison to other metal casting techniques.
- The expensive expense of patterning dies has historically restricted investment casting to large volumes of production
- The high cost is also due to the need for specific equipment, expensive material refractory and high labor costs.
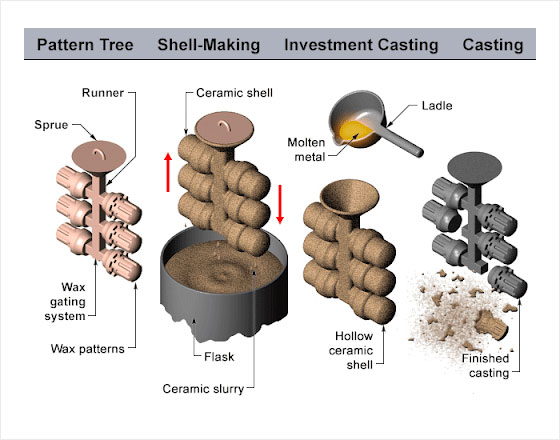