Processes
- Polymer Processing
- Injection Molding Insert Molding Blow Molding Over Molding Metal Injection Molding Thermoforming
- Metal Casting
- Die Casting Castings & Forgings Wax Casting Lost Wax Casting Grey Iron Castings Centrifugal Casting Investment Casting Permanent Mold Sand Casting Shell Mold Casting Aluminum Investment Casting Brass Investment Casting Steel Investment Castings Titanium Investment Casting
- Machining
- Milling Turning EDM machining CNC Engraving Hole-making Tap Size Chart Drill Size Chart 5 axis machining Micro Machining CNC Cutting Metal Processes Ceramic Manufacturing Swiss Precision Machining
Materials
Permanent Mold Casting – What Is Permanent Mold Casting?
Permanent mold casting refers to the usage of the same mold for each casting cycle, as opposed to sand casting when the form is torn away after each use. Although the mold is not really “permanent,” it will deteriorate over time and will ultimately need to be reconditioned or replaced, as with any process and equipment. The term refers to the mold’s habit of being utilized again. When compared to metal solidified by sand casting, another common casting technique, permanent mold casting provides metal with greater dimensional accuracy, superior surface polish, and higher and more consistent mechanical characteristics.
Types Of Permanent Mold Casting
Permanent mold casting is classified into four types: Vacuum, Slush, Gravity & Low Pressure.
1.Vacuum
Vacuum permanent mold casting maintains all of the benefits of LPPM casting, plus dissolved gases in the molten metal are reduced and molten metal purity is improved. The technique is capable of handling thin-walled profiles and produces a good surface finish. Mechanical characteristics are typically 10 to 15% better than those of gravity permanent mold castings. The weight of the procedure is restricted to 0.2 to 5 kg (0.44 to 11.02 lb).
2.Slush
Slush casting is a kind of permanent molding casting used to make hollow castings or hollow casts. The material is poured into the mold and allowed to cool until a shell of material develops in the mold throughout the process. The remainder of the liquid is then drained out, leaving a hollow shell. The finished casting has excellent surface detail, although the wall thickness varies. The technique is often used to cast decorative items from low-melting-point materials, including candlesticks, lamp bases, and statues. Hollow chocolate figurines for Easter and Christmas are made using a similar method. It utilizes less material than solid casting, resulting in a lighter and more affordable product. In general, hollow cast figurines feature a tiny hole where the surplus liquid was poured out. Similarly, slush molding is used in the production of automobile dashboards for soft-panel interiors with fake leather, where a free-flowing (like a liquid) powder plastic compound, either PVC or TPU, is poured into a heated, hollow mold and a viscous skin develops. Excess slush is then drained from the mold, the mold is cooled, and the formed object is removed.
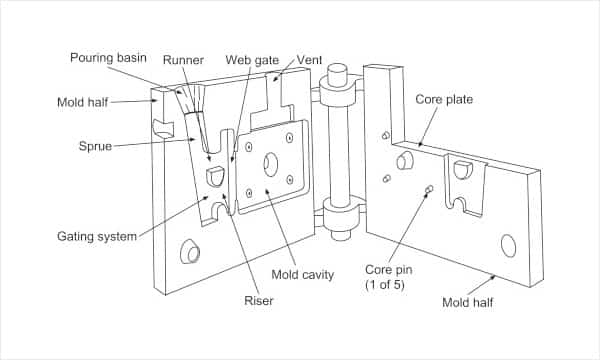
3.Gravity
To smooth the flow and minimize thermal damage to the casting, the gravity process starts by preheating the mold to 150-200°C (300-400°F). The molding chamber is subsequently covered with a refractory substance or a mold wash to prevent the casting from adhering to the mold and to extend mold life. The mold is then fastened shut and any sand or metal cores are inserted. The mold is then filled with molten metal. To minimize the possibility of hot tears, the mold is opened soon after solidification and the casting is removed. The procedure is then repeated, but this time no preheating is needed since the heat from the last casting is sufficient, and the refractory coating should endure for many castings. Because this procedure is typically done on big production runs, automated equipment is utilized to coat the mold, pour the metal, and remove the casting. To reduce fractures and porosity, the metal is poured at the lowest possible temperature. The pouring temperature varies significantly depending on the casting material; for example, zinc alloys are poured at about 370°C(698°F), whereas gray iron is poured at around 1,370°C(2,500°F).
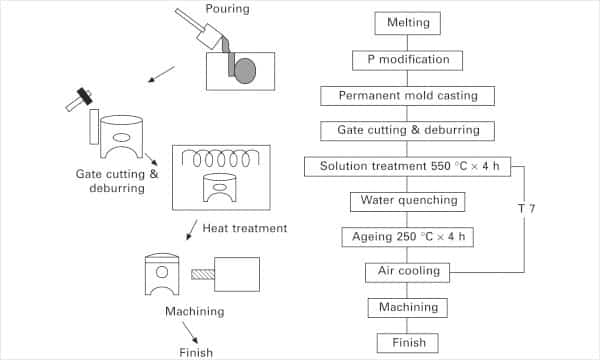
4.Low-pressure
The low-pressure permanent mold casting process is shown schematically. Low-pressure permanent mold (LPPM) casting employs a low-pressure gas, typically between 3 and 15 psi (20 to 100 kPa), to force molten metal into the mold cavity. Pressure is exerted to the pool’s surface, forcing the molten metal up a refractory pouring tube and ultimately into the mold’s bottom. Because the pouring tube reaches all the way to the bottom of the ladle, the material being forced into the mold is extremely clean. Because the applied pressure pushes molten metal in to compensate for shrinkage, no risers are needed. Because there is no riser, any metal in the pouring tube simply falls back into the ladle for reuse, yields are often higher than 85%. The bulk of LPPM castings are made of aluminum and magnesium, although some are made of copper alloys. Because of the constant pressure, there is very little turbulence while filling the mold, which reduces gas porosity and dross development. Mechanical characteristics are approximately 5% better than those of gravity permanent mold castings. The drawback is that the cycle periods are greater than those of gravity permanent mold castings.
The Permanent Mold Casting Process – How Does Permanent Mold Casting Work?
In general, the permanent mold casting method is based on the same principles as any other casting technique: A molten raw material is injected into a mold cavity, cooled, and then withdrawn from the mold. In the case of permanent molds, the mold is made in two parts and then split once the material has cooled.
- Mold Creation: A permanent mold will be built around a pattern, which is a single piece in the shape to be cast that is usually produced via machining. Permanent molds are often constructed of iron or steel.
- Mold Pre-heating: After the mold is constructed and the process begins, it will be warmed to enable the molten material to flow easily through the mold without premature cooling and solidification. Preheating provides the advantage of dampening some of the thermal shocks that occur naturally with molten material. A “cold” mold would respond considerably more severely to the huge variation in raw material temperature.
- Optional Core Placement: To create component characteristics like cavities and undercuts, cores may be inserted inside a permanent mold. The liquid raw material (such as aluminum) is injected into the mold cavity through one or more sprues during this phase. While gravity may be used to complete this process, alternative techniques like low-pressure casting and vacuum casting are also possible.
- Cooling: A minimum cooling time is needed for complete solidification based on the size and form of each component. The third and last phase happens after the cooling period has been achieved.
- Component Removal/Ejection: As previously stated, permanent molds are made in two parts that are separated after the part has hardened fully and is ready to be removed. To keep the component from adhering to the mold, the inner surfaces of the cavity are occasionally covered with a substance. The mold may also include ejector pins. Following the ejection, any extra material, such as flash or runner material, will be cut. Parts will then be transferred through procedures such as heat treatment, aging, and other finishing needs.
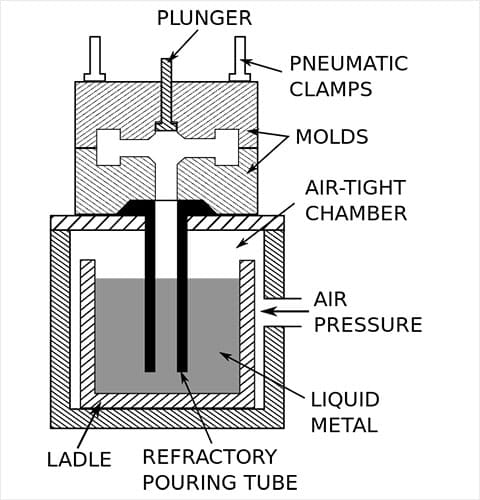
Applications Of Permanent Mold Casting Process
The technique is often used for components that need increased strength and longevity. Permanent mold cast components are often used in the following applications:
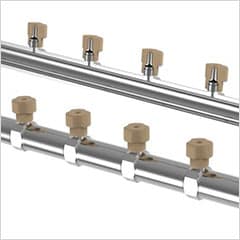
Manifolds
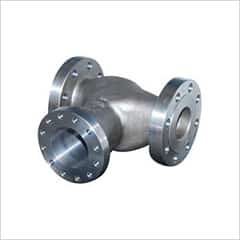
Body of a valve
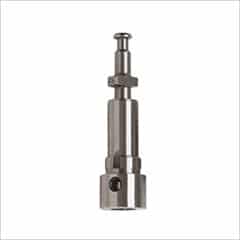
Pump elements
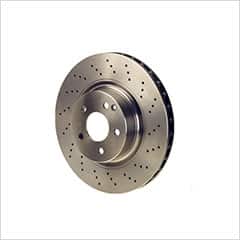
Castings for brakes

Castings for inserts
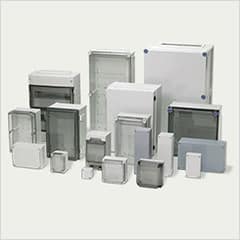
Electronic enclosures
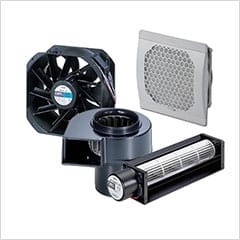
HVAC and ventilation components(fan blades & blowers)
Benefits Of Permanent Mold Casting Process
The reusable mold, excellent surface quality, dimensional precision, and high production rates are the primary benefits. Tolerances are typically 0.4 mm for the first 25 mm (0.015 inches) and 0.02 mm for each subsequent centimeter (0.002 inches per inch); if the dimension passes the parting line, add 0.25 mm (0.0098 in). Surface finishes range from 2.5 to 7.5 m (100-250 in) RMS. A draft of 2 to 3 degrees is needed. The thickness of the walls is restricted to 3 to 50 mm (0.12 to 1.97 in). Part sizes typically vary from 100 g to 75 kg (several ounces to 150 lb). Other benefits include the simplicity with which directed solidification may be induced by altering the thickness of the mold wall or by heating or cooling parts of the mold. The use of a metal mold results in a finer grain structure than sand casting because of the faster cooling rates. Undercuts may be created using retractable metal cores while retaining a fast-action mold. and if you’re debating between sand and permanent mold casting, the following benefits of permanent mold casting may help you decide:
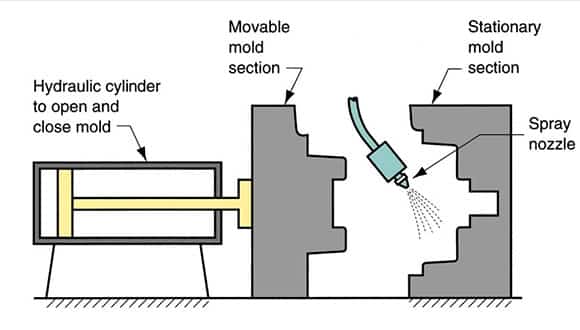
- The porosity of a sand mold contributes to the final part’s weakness. Permanent molds made of iron or steel do not have this problem.
- When compared to sand casting, parts produced via permanent mold casting have a smoother surface. Polishing, for example, may be used to improve the smoothness of any casting process.
- Permanent molds may manufacture components with tighter tolerances than sand.
- Permanent molds may last for more than 50,000 cycles, depending on the material used in casting, the pouring temperature, mold maintenance, and other factors.
Drawbacks Of Permanent Mold Casting Process
There are three major drawbacks: expensive tooling costs, a restricted selection of low melting-point metals, and short mold life. Because of the high tooling costs, this method is uneconomical for short production runs. The mold life is very short when the technique is used to cast steel or iron. Mold life is greater for lower melting point metals, however thermal stress and erosion typically restrict the life to 10,000 to 120,000 cycles. Mold life is determined by four factors: mold material, pouring temperature, mold temperature, and mold design. Molds constructed of gray cast iron are less expensive to manufacture but have a shorter mold life. Molds constructed of H13 tool steel, on the other hand, may have a mold life that is many times higher. The pouring temperature is determined by the casting metal; nevertheless, the greater the pouring temperature, the shorter the mold life. A high pouring temperature may also cause shrinkage issues and lengthen cycle times. Misruns are generated if the mold temperature is too low, but if the mold temperature is too high, the cycle time is extended and mold erosion is enhanced. Large variations in section thickness in the mold or casting may also shorten mold life.
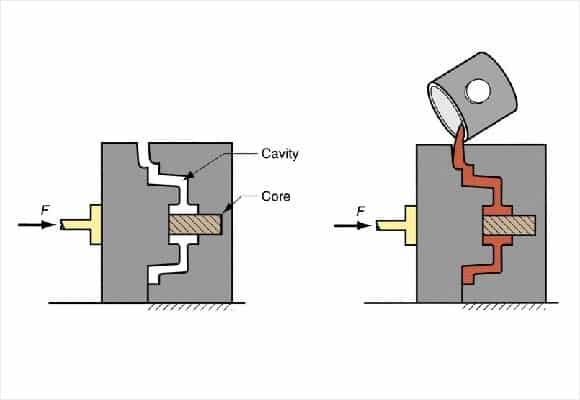