Processes
- Polymer Processing
- Injection Molding Insert Molding Blow Molding Over Molding Metal Injection Molding Thermoforming
- Metal Casting
- Die Casting Castings & Forgings Wax Casting Lost Wax Casting Grey Iron Castings Centrifugal Casting Investment Casting Permanent Mold Sand Casting Shell Mold Casting Aluminum Investment Casting Brass Investment Casting Steel Investment Castings Titanium Investment Casting
- Machining
- Milling Turning EDM machining CNC Engraving Hole-making Tap Size Chart Drill Size Chart 5 axis machining Micro Machining CNC Cutting Metal Processes Ceramic Manufacturing Swiss Precision Machining
Materials
What is Swiss Machining & Swiss Precision Machining
Swiss machining is a manufacturing method using a specialized tool and feeding method to machine the stock into complex or intricate parts with tight tolerances. Swiss precision machining involves the use of Swiss-type CNC lathes that turns parts in a radial motion when the workpiece is being cut. The Swiss machining and the Swiss-type machine are developed in Switzerland in the 19th century due to the demand on Swiss watchmakers, which has made it different from other conventional lathes when fabricating small complex parts, the inventor of the Swiss machine is Jakob Schweizer, he conceived a new method of sliding parts along the longitudinal axis of the lathe instead of moving parts down the tool rest, this allows tiny diameters accurately to be machined, the principle of original Swiss lathe machine still apply nowadays, the development of CNC programming assists its operation. Swiss precision machining and Swiss turning are cost-effective ways for the high volume of small, complex parts.
How Does Swiss Machining Work?
The most distinctive feature of Swiss precision machining is the utilization of a gang tool post and guide bushing, which can make the cutting tool in close contact with the material, minimizes the part deflection, and increases the precision, as well as maintains tight tolerances. During the Swiss machining, the feeding of bar stock to the processing area is completed by the guide bushing, which also supports the workpiece firmly. The Swiss machine moves the bar stock through guide bushing using a sliding headstock, which moves forward and backward, only exposes the part of the workpiece being machined travels to the tooling area, in order to hold the part tightly in place for improving stability and precision.
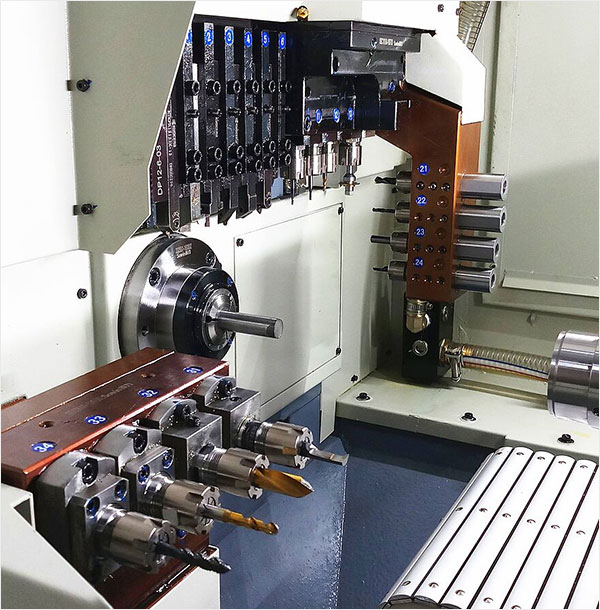
What is a Swiss CNC Machine?
A Swiss CNC machine, a Swiss machine with automation, also known as Swiss type lathe and Swiss screw machine, is a modern precision manufacturing machine tool that can produce small parts with high efficiency and accuracy. The most obvious difference between Swiss CNC lathe and traditional CNC lathe is that the workpiece on a Swiss machine can rotate and move back and forth along the Z-axis, and multiple operations can be performed simultaneously, while on a traditional lathe machine, the material can only rotate in a fixed position and be held in one or both ends, generally, only one operation can be done once. Swiss CNC machines can be used to produce turned parts and complex components without turned surfaces.
Materials Used in Swiss Precision Machining
A diversity of metals and other types of materials can be machined with Swiss CNC machining, depending on the required features, properties, and specifications. Common options including:
- Steel, Stainless steel, Carbon steel, Tool steel
- Brass, Bronze, Copper
- Titanium
- Other alloys
- Plastics
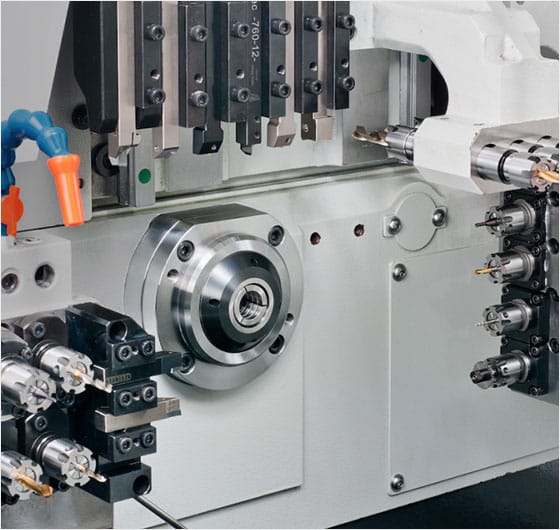
Benefits & Advantages of Swiss Precision Machining
- Improved productivity. Swiss screw machine utilizes CNC unit to machine the desired part, the programmed instruction can reduce manual operation and errors, in addition, several operations can be done at the same time, the strong capabilities of Swiss machining allows a large number of parts to be machined at a shorter time, which improves the efficiency and productivity. The cycle time for a Swiss CNC machine can be significantly shorter than other types of CNC machines.
- Tight tolerances. Swiss machine firmly supports the workpiece next to the processing area, the part keeps stability and almost not affected by tooling force. In this way, even when machining very small parts, it can ensure that the precision is within a very strict tolerance range.
- Lower cost. Swiss type lathes accommodate bar stocks with smaller sizes, then machined components manufacturers can stock smaller materials at a lower cost. On the other hand, the automation of Swiss CNC machining also reduces the labor cost the shortens the lead time.
- High versatility. Not only can Swiss machines be used to process smaller parts, but they are also capable to produce parts that are longer, slender, and more complex. Swiss machines can also produce intricate parts with thinner walls, more delicate features, and deeper cuts that are difficult or impossible on other machines.
- Fewer secondary processing. Swiss machining parts generally have fine detail and a good surface finish, which reduces the need for post-processing or operations, and the parts that are ready to ship after the machining.
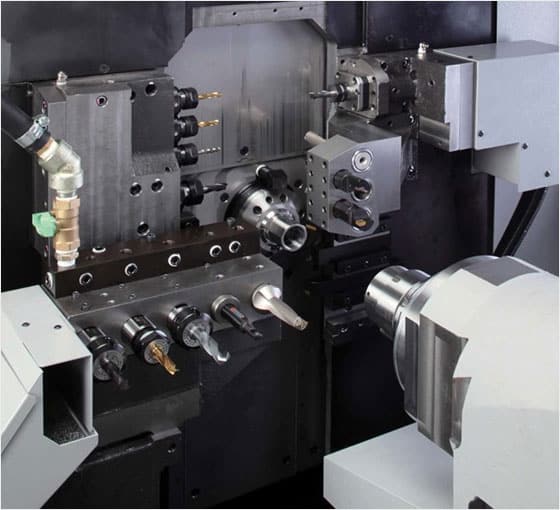
Applications of Swiss CNC Machining
The Swiss machine is originally developed for the manufacturing of screws used in the watchmaking industry, even though they still can fabricate parts for watches, because of the ability of Swiss lathe on the production of extremely small precise parts with a fast speed, now modern Swiss machining has become popular for products in a variety of industries. Implants, shafts, contact pins, housings, inserts, and sockets are commonly created through Swiss machining.
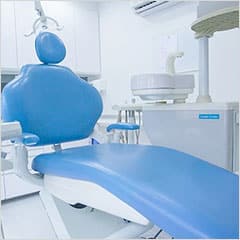
Medical and dental
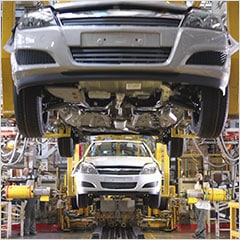
Automotive and vehicles
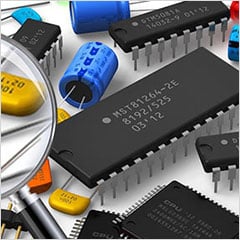
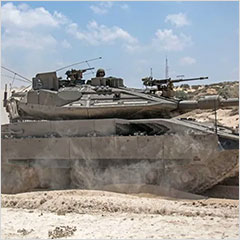
Military vehicles and systems
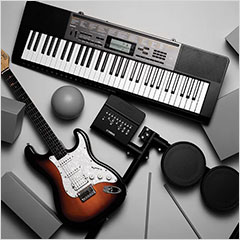
Musical instruments
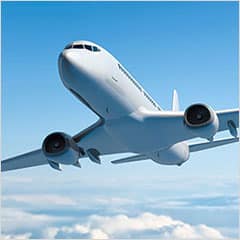
Aerospace and defense
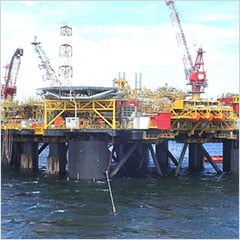
Oil and energy
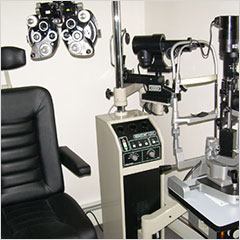
Optical equipment
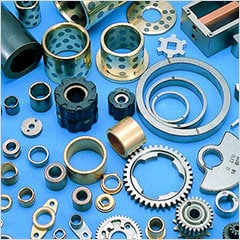
Mechanical parts