Processes
- Polymer Processing
- Injection Molding Insert Molding Blow Molding Over Molding Metal Injection Molding Thermoforming
- Metal Casting
- Die Casting Castings & Forgings Wax Casting Lost Wax Casting Grey Iron Castings Centrifugal Casting Investment Casting Permanent Mold Sand Casting Shell Mold Casting Aluminum Investment Casting Brass Investment Casting Steel Investment Castings Titanium Investment Casting
- Machining
- Milling Turning EDM machining CNC Engraving Hole-making Tap Size Chart Drill Size Chart 5 axis machining Micro Machining CNC Cutting Metal Processes Ceramic Manufacturing Swiss Precision Machining
Materials
What Is Thermoforming
It is a special plastic processing method to process thermoplastic sheet into various products. The sheet is clamped on the frame and heated to the softening state. Under the action of external force, the sheet is close to the mold surface to obtain the shape similar to the mold surface. After cooling and shaping, the product is finished after trimming. This process is also used for rubber processing. In recent years, thermoforming has made new progress, such as continuous production technology from extrusion sheet to thermoforming.
In the market, there are more and more thermoforming products, such as cups, dishes, food plates, toys, helmets, as well as auto parts, building decoration, chemical equipment, etc. Compared with injection molding, thermoforming has the advantages of high production efficiency, less equipment investment and large surface area.
Pros of thermoforming:
Can produce very large parts
High production rate
Low cost
Cons of thermoforming:
Limited shape complexity
Limited to thin walled parts
Scrap cannot be recycled
Trimming is required
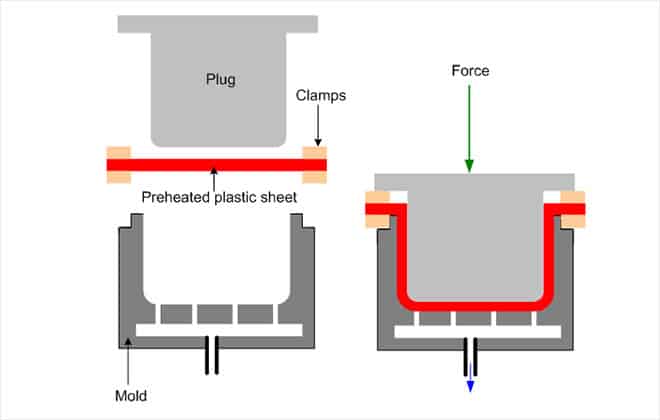
Plastic Used For Thermoforming
The plastics used for thermoforming mainly include:
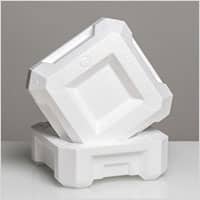
Polystyrene (PS)
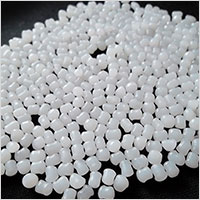
Polypropylene (PP)
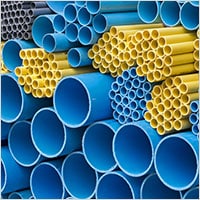
Polyvinyl Chloride (PVC)
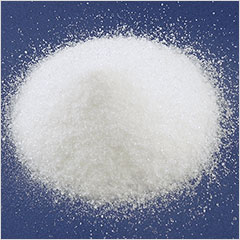
Polyacrylate (such as Polymethylmethacrylate)
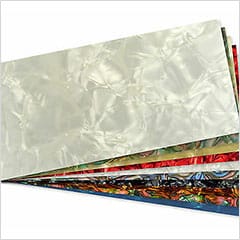
Cellulose (such as Nitrocellulose, Cellulose Acetate, etc.)
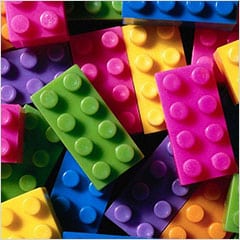
Engineering plastics (such as ABS, Polycarbonate)
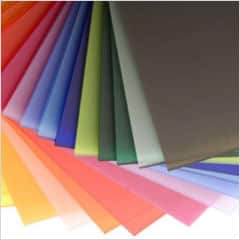
Acrylic (PMMA)
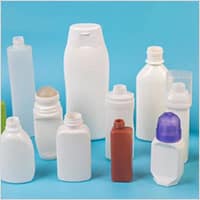
Low Density Polyethylene (LDPE)
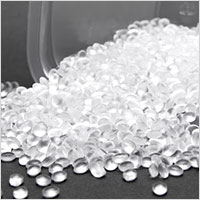
High Density Polyethylene (HDPE)
Types Of Thermoforming
There are many kinds of thermoforming methods, but they are basically based on the combination or improvement of vacuum, air pressure or mechanical pressure.
- Vacuum forming: Vacuum is used to make the heat softened sheet close to the mold surface. This method is the simplest, but the pressure difference caused by vacuumizing is not big, so it is only used for products with simple appearance.
- Pressure forming: Compressed air or steam pressure is used to force the heated and softened sheet to form close to the surface of the die. Because the pressure difference is larger than that of vacuum forming, the products with complex shape can be manufactured.
- Mechanical forming: The thermoplastic sheet is mechanically forced into or around the mold by direct contact. Typically, a core plug will push the sheet into the mold cavity and force it into the desired shape.
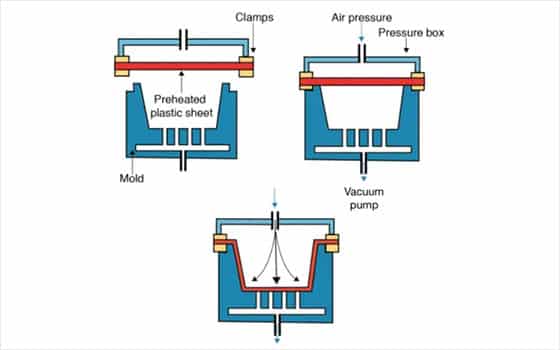
Other thermoforming types:
Mold to mold thermoforming: The heat softened sheet is placed between a pair of female and male molds and formed by mechanical pressure. This method has higher forming pressure and can be used to manufacture products with complex shape, but the cost of mould is higher.
Plunger assisted pressure forming: The heated sheet is partially pre stretched by a plunger or a male die, and then molded by vacuum or air pressure to produce products with large depth and uniform wall thickness distribution.
- Solid state molding: The sheet is heated to a temperature not exceeding the melting point of the resin to keep the material in a solid state for molding. Used for ABS resin, polypropylene, high molecular weight high density polyethylene. The rigidity and strength of the parts are higher than those of the general thermoforming products.
- Double sheet thermoforming: It is a kind of special processing method to process thermoplastic sheet materials into various products. The sheet is clamped on the frame and heated to a softened state. Under the action of external force, the sheet is close to the mold surface. After cooling and setting, the product is obtained. This method is also used in rubber processing. Compared with injection molding, it has high production efficiency, The main plastics used are polystyrene, polyvinyl chloride, polyolefin, etc. there are many molding methods, which are based on the combination or improvement of vacuum, air pressure or mechanical pressure. It can be used to produce food utensils, toys, helmets, automobile parts, architectural ornaments, chemical equipment, etc.
Capabilities Of Thermoforming
- Shapes:Thin-walled: Cylindrical, Cubic, Complex
- Part size:Area: 0.04 in² – 300 ft²
- Materials: Thermoplastics
- Surface finish – Ra: 60 – 120 μin
- Tolerance: ± 0.04 in.
- Max wall thickness: 0.015 – 0.15 in.
- Quantity: 10 – 1000
- Lead time: Days
- Applications: Packaging, open containers, panels, cups, signs
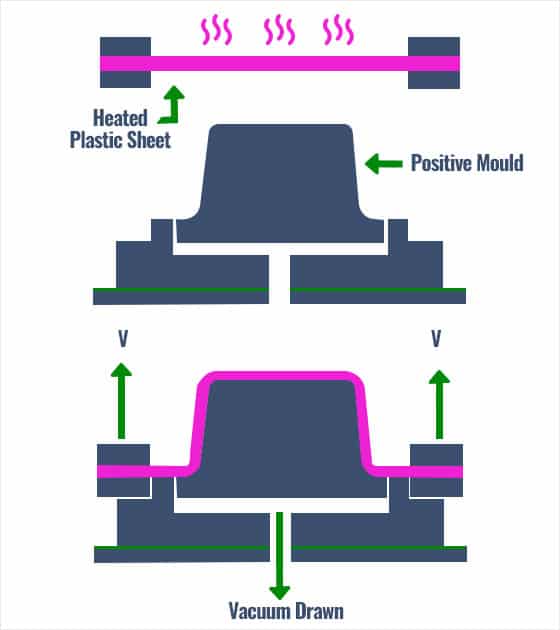
Thermoforming Capabilities | ||
---|---|---|
Typical | Feasible | |
Shapes: | Thin-walled: Cylindrical Thin-walled: Cubic Thin-walled: Complex |
|
Part size: | Area: 0.04 in² – 300 ft² | |
Materials: | Thermoplastics |
|
Max wall thickness: | 0.015 – 0.15 in. | 0.002 – 0.25 in. |
Advantages: | Can produce very large parts High production rate Low cost |
|
Disadvantages: | Limited shape complexity Need to trim Thin-walled parts only Waste cannot be recycled |
|
Applications: | Cups, packaging, panels, open containers |