Processes
- Polymer Processing
- Injection Molding Insert Molding Blow Molding Over Molding Metal Injection Molding Thermoforming
- Metal Casting
- Die Casting Castings & Forgings Wax Casting Lost Wax Casting Grey Iron Castings Centrifugal Casting Investment Casting Permanent Mold Sand Casting Shell Mold Casting Aluminum Investment Casting Brass Investment Casting Steel Investment Castings Titanium Investment Casting
- Machining
- Milling Turning EDM machining CNC Engraving Hole-making Tap Size Chart Drill Size Chart 5 axis machining Micro Machining CNC Cutting Metal Processes Ceramic Manufacturing Swiss Precision Machining
Materials
What Is Sand Casting And How Does It Work
Sand casting is a widely used casting form. As the name suggests, it’s making molds out of sand. In sand casting, the finished part model needs to be put into the sand. The mold is then filled with sand at the end of the mold to form a mold. If it is necessary to remove the mould before casting metal, the mould shall be made into two or more parts. The mold must be modified to have holes for casting metal into the mold. The mold is held for a suitable time until the metal solidifies. After the part is removed, the mold is destroyed, so a new mold must be made for each casting. Sand mold processing plant can cast large parts. Sand mold can be used in iron casting, bronze casting, brass casting and aluminum casting. Wet mold casting is another kind of sand mold casting process, which has low cost and can produce parts of various sizes.
Some smaller sand cast parts include components as gears, pulleys, crankshafts, connecting rods, and propellers. Larger applications include housings for large equipment and heavy machine bases. Sand casting is also common in producing automobile components, such as engine blocks, engine manifolds, cylinder heads, and transmission cases.
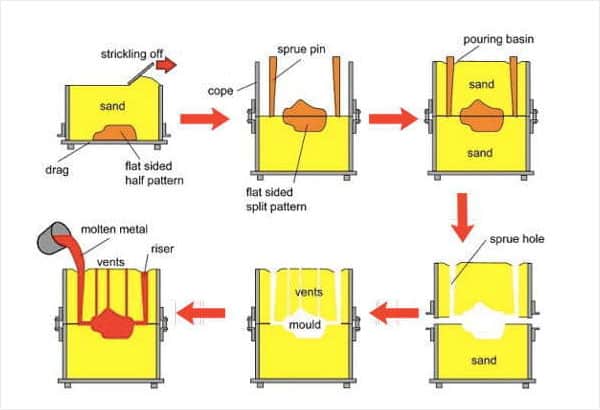
Materials Of Sand Casting
Sand casting is able to make use of almost any alloy. An advantage of sand casting is the ability to cast materials with high melting temperatures, including steel, nickel, and titanium. The four most common materials that are used in sand casting are:
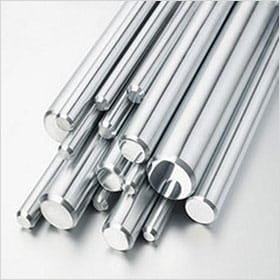
Aluminum alloys
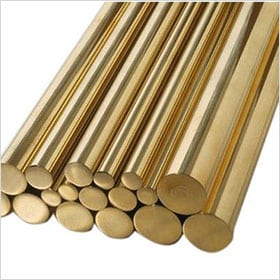
Brass alloys
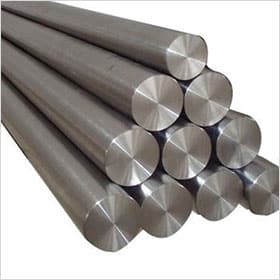
Cast iron
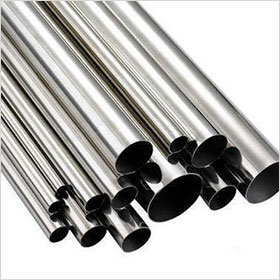
Cast steel
Sand Casting Process
1. Drawing of sand casting
The traditional method is to get the casting drawings and send them to the foundry. This process can be completed in the quotation. Nowadays, more and more customers and foundry manufacturers use CAD instead of CAD.
2. Mold
In sand casting, the mold is made of wood or other metal materials. In this process, we ask our engineers to make the mold size slightly larger than the finished product, and the difference is called shrinkage allowance. The purpose is that the molten metal acts on the mold to ensure solidification and shrinkage of the molten metal, so as to prevent voids in the casting process.
3. Core making
For core making, the resin sand is put into the mold to form the casting with internal surface. Therefore, the gap between the core and the mold becomes the final casting.
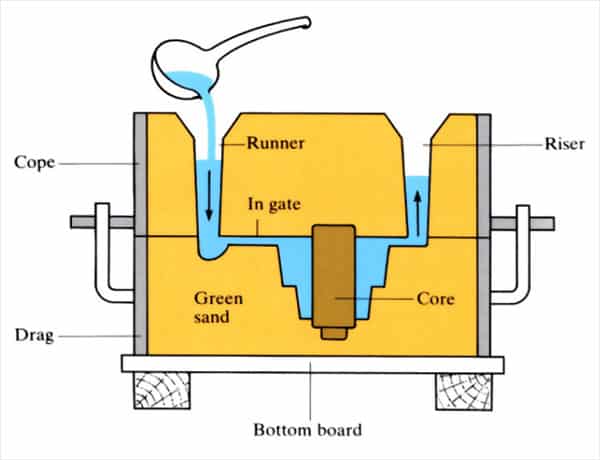
4. Forming
In the process of melting and forming, a pair of mould needs to be prepared. Molding usually involves the support frame of the mold, pulling out the mold to separate it during casting, melting the previously placed core in the mold, and then closing the mold opening.
5.Cleaning
The purpose of cleaning is to remove grit, grind and excess metal from the casting. Welding and desanding can improve the surface appearance of castings.
Advantages Of Sand Casting
- The dimensional accuracy of sand castings is high. After the mold is finished, there is no mold, no parting, no casting slope and live block, in many cases the sand core is eliminated, and sometimes the sand core is only used to make horizontal small holes.
- Increase the degree of freedom of sand casting parts design and change the connotation of sand casting to the casting structure process. Product designers can design the structure of castings according to the overall needs, increasing the degree of freedom of sand casting parts design.
- Simplify the production process of sand castings, shorten the production cycle, increase labor productivity, reduce labor intensity, and improve working conditions.
- The sand castings are of good quality, with high dimensional accuracy, no burrs and burrs, and low rejection rate. Reduce material consumption and reduce the cost of castings.
Applications Of Sand Casting
- Engine blocks and manifolds,
- Machine bases
- Gears
- Pulleys
Possible Defects Of Sand Casting
Unfilled sections
- Insufficient material
- Low pouring temperature
Porosity
- Melt temperature is too high
- Non-uniform cooling rate
- Sand has low permeability
Hot tearing
- Non-uniform cooling rate
Surface projections
- Erosion of sand mold interior
- A crack in the sand mold
- Mold halves shift
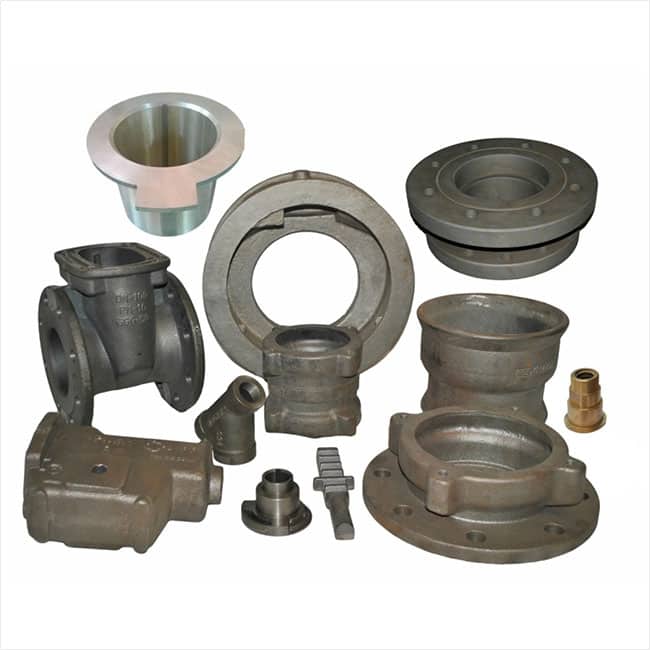
Cost Drivers For Sand Casting
Material cost
The cost of materials for sand casting includes the cost of the metal, the cost of melting the metal, the cost of the mold sand, and the cost of the core sand. This is determined by the weight of the part, which is computed based on its volume and density, as well as the unit price of the material used in the manufacturing process. It is also true that the melting cost will be higher for heavier parts, and this is impacted by the material used, as some materials are more expensive to melt than others. The melting cost, on the other hand, is often low when compared to the metal cost. Weight of the part has a direct relationship with the amount of mold sand that is used and, consequently, the cost of the part. In the end, the cost of core sand is determined by the number and size of the cores utilized in the casting process of the part.
Production cost
The cost of manufacturing the item covers a number of processes that are required to cast the part, such as core-making, mold-making, pouring, and cleanup. The cost of producing the cores is determined by the volume of cores produced and the quantity of cores used in the casting process. With the use of automated equipment, the cost of mold-making is not significantly affected by the geometry of the part. The presence of cores, on the other hand, will slightly slow down the process and consequently raise the cost. Finally, the weight of the item influences both the cost of pouring the metal and the cost of cleaning the final casting when it has been finished. A larger and heavier casting will take longer to pour and clean, as well as to finish.
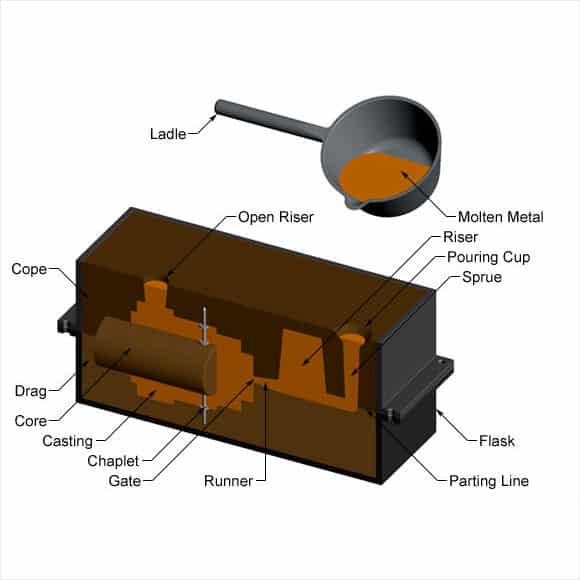
Tooling cost
The pattern and the core boxes are the two most important components of the tooling cost. The cost of the pattern is mostly determined by the size of the part (both the envelope and the estimated area), as well as the complexity of the part being produced. The cost of the core-boxes is determined first by their size, which is determined by the amount and size of the cores that are utilized in the casting process. The complexity of the cores, like the pattern, will have an impact on the time it takes to create this component of the tooling (in addition to the size of the core), and therefore the cost.
The amount of pieces that are cast will also have an impact on the cost of tooling. The use of a tooling material that will not wear under the required number of cycles will be required for a bigger manufacturing quantity, both for the pattern and core-boxes. A stronger, more lasting tooling material will be used, which will result in a large increase in the cost.