Processes
- Polymer Processing
- Injection Molding Insert Molding Blow Molding Over Molding Metal Injection Molding Thermoforming
- Metal Casting
- Die Casting Castings & Forgings Wax Casting Lost Wax Casting Grey Iron Castings Centrifugal Casting Investment Casting Permanent Mold Sand Casting Shell Mold Casting Aluminum Investment Casting Brass Investment Casting Steel Investment Castings Titanium Investment Casting
- Machining
- Milling Turning EDM machining CNC Engraving Hole-making Tap Size Chart Drill Size Chart 5 axis machining Micro Machining CNC Cutting Metal Processes Ceramic Manufacturing Swiss Precision Machining
Materials
Sheet Metal Cutting (Shearing)
Metal Cutting is one of the most important processes in the sheet metal fabrication industry, while shearing is the most common sheet metal cutting processes which performed by means of machines called shears, which consist of blades that act on the metal making a cut.
Sheet metal cutting is an operation of great importance in the manufacturing processes for different sectors of the industry. This operation is carried out on materials such as steel, where each material is obtained through a preliminary process. In addition, for the final product to be transformed, it must undergo a transformation, where this cut plays a very important role. With the development of technology, we have more metal cutting methods, but the shearing cut is always the most traditional and widely used one.
What Is Shear Cutting ?
Sheet metal shear cutting is a mechanical process of straight cutting of sheet metal that is characterized by using two blades that slide against each other. It is based on a crushing, followed by a partial penetration cut into the surface of the part. Ending with the fracture of the rest of the cutting section without chip removal.
History of Shearing
For cutting sheet metal or strip, the shears have been the basic instrument for centuries. As a manual instrument, the use of the scissors dates back to the Bronze Age. In its beginnings it was a sheet of metal bent in a U-shape and only from the 14th century did pivot scissors appear, with the two blades moving around an axis. The so-called lever shear or scissors, operated manually, allowed to cut thicknesses of up to 5 mm and could also be operated by pedal.
The technology associated with sheet metal cutting did not turn around until the mid-nineteenth century, when the first steam-powered shear was designed and built, using a crank-and-flywheel connecting rod system, to cut thick slab. In the following decades, increasingly powerful and sophisticated shears were built, equipped with several blades or combined with punching machines, as already described.
The so-called unconventional processes for sheet metal cutting (beam cutting processes): cutting by water or air jet, oxyfuel, plasma arc or laser, are technologies developed entirely during the 20th century.
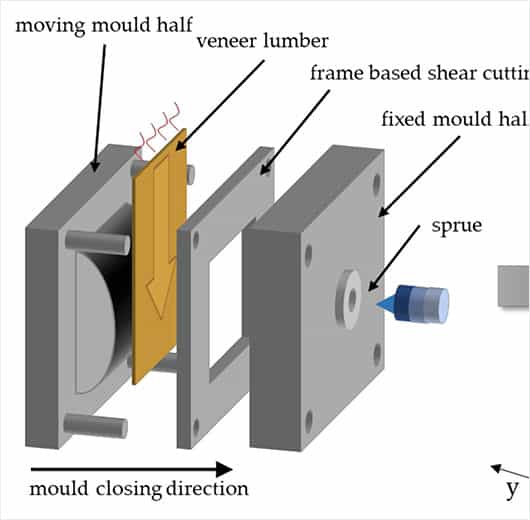
Shearing Process
It is a cold process in which the pieces are cut by applying equal shear forces to the sheet but in the opposite direction. To shear a sheet metal you have to use two sharp blades, sliding one against the other. The shear cutting process occurs just before the upper blade comes into contact with the mechanical material. Just at that moment the metal sheet begins to be pressed, proceeding to its deformation. In this way, the entire piece is fractured, separating the sheet.
Shearing is commonly used to produce straight line cuts but angled cuts can be made as well, is primarily used to cut sheet stock into smaller sizes in preparation for other processes.
Shearing Features
Sheet thickness: 0.005-0.25 inches
Tolerance: ±0.1 inches (±0.005 inches feasible)
Surface finish: 250-1000 μin (125-2000 μin feasible)
Shear Machine & Types
Shear is a machine or tool to perform shearing cut for sheet metal, which is also known as squaring shear or power shear. A shear can be operated manually (by hand or foot) or by hydraulic, pneumatic, or electric power. So we can find different varieties of shears. As we mentioned before, in manual shears, the operator or worker is in charge of carrying out the movement and exerting pressure on the blade to perform the cut. Although there are automated. We will have to choose the one that best suits our needs depending on the work that is going to be carried out and according to its required specificities.
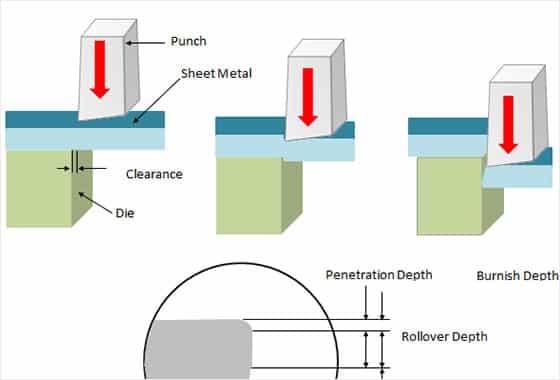
How To Do Sheet Metal Cutting With Shear?
Shearing is a mechanical process used to cut straight on sheet metal. A material is cut between the edges of two opposing cutting tools. First, the material is blocked; When the workpiece is fixed, a movable knife descends towards a fixed knife with the space between them determined by the required displacement. The movable knife can be adjusted at an angle to cut material progressively from side to side: this angle is indicated as cutting angle and reduces the force required, but increases the knife stroke.
The basic components of a guillotine shear are the bench, a clamping device for the piece to be machined called the sheet, the upper and lower blade and a reference device called the back gauge, used to ensure the workpiece is cut where needed. Very common is a back support that supports the workpiece, with eventual automatic unloading or stacking.
To make a perfect cut, a high-quality shear is required that minimizes the effects of varying sheet metal composition, built-up internal stresses, and geometry. These natural effects, if not corrected and compensated for, become defects in the finished products, reducing their quality.
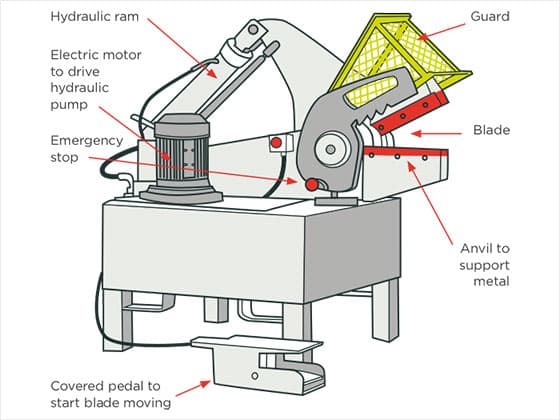