Processes
- Polymer Processing
- Injection Molding Insert Molding Blow Molding Over Molding Metal Injection Molding Thermoforming
- Metal Casting
- Die Casting Castings & Forgings Wax Casting Lost Wax Casting Grey Iron Castings Centrifugal Casting Investment Casting Permanent Mold Sand Casting Shell Mold Casting Aluminum Investment Casting Brass Investment Casting Steel Investment Castings Titanium Investment Casting
- Machining
- Milling Turning EDM machining CNC Engraving Hole-making Tap Size Chart Drill Size Chart 5 axis machining Micro Machining CNC Cutting Metal Processes Ceramic Manufacturing Swiss Precision Machining
Materials
What Is Injection Molding
Injection mold is a tool to produce plastic products. It is also a tool to give plastic products complete structure and precise size. Injection molding is a kind of processing method used in batch production of some complex shape parts. Specifically, the heated and melted plastic is injected into the mold cavity by the injection molding machine under high pressure, and the formed product is obtained after cooling and curing.
Injection mold can be divided into thermosetting plastic mold and thermoplastic plastic mold according to molding characteristics. According to the molding process, it can be divided into transfer mold, blowing mold, casting mold, hot forming mold, hot pressing mold (pressing mold), injection mold, etc. the hot pressing mold can be divided into overflow, semi overflow and non overflow by the way of overflow, and the injection mold can be divided into cold runner mold and hot runner mold by the way of gating system; According to the loading and unloading methods, it can be divided into mobile type and fixed type.
Advantages:
- Can form complex shapes and fine details
- Excellent surrface finish
- Good dimensional accuracy
- High production rate
- Low labor cost
- Scrap can be recycled
Disadvantages:
- Limited to thin walled parts
- High tooling and equipment cost
- Long lead time possible
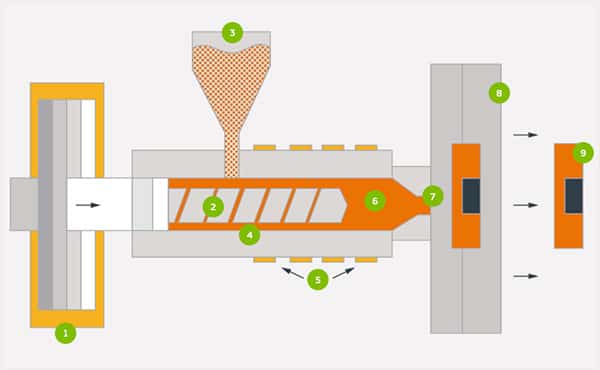
Injection Molding Types
Although the structure of the mold may vary due to the variety and performance of plastics, the shape and structure of plastic products and the type of injection machine, the basic structure is the same. The mould is mainly composed of gating system, temperature regulating system, forming parts and structural parts. Among them, the gating system and molding parts are the parts that directly contact with plastics and change with plastics and products, which are the most complex and changeable parts in the plastic mold and require the highest machining finish and precision.
Composition Of Injection Molding
The injection mold is composed of moving mold and fixed mold. The moving mold is installed on the moving template of the injection molding machine, and the fixed mold is installed on the fixed template of the injection molding machine. In injection molding, the moving mold and the fixed mold are closed to form the gating system and the cavity. When the mold is opened, the moving mold and the fixed mold are separated to take out the plastic products. In order to reduce the heavy workload of mold design and manufacturing, the injection mold mostly adopts the standard mold base.
1.Gating System
Gating system refers to the part of the runner before the plastic enters the cavity from the nozzle, including the sprue, cold cavity, splitter and gate.
Gating system, also known as runner system, is a group of feeding channels leading the plastic melt from the nozzle of the injection molding machine to the cavity, which is usually composed of main flow channel, shunt channel, gate and cold material cavity. It is directly related to the molding quality and production efficiency of plastic products.
2.Temperature Regulating System
In order to meet the requirements of injection process for mold temperature, a temperature regulating system is needed to adjust the mold temperature. For thermoplastic injection mold, the cooling system is designed to cool the mold. The common method of mold cooling is to set up cooling water channel in the mold, and use the circulating cooling water to take away the heat of the mold; In addition to hot water or steam in cooling water channel, electric heating elements can be installed inside and around the mold.
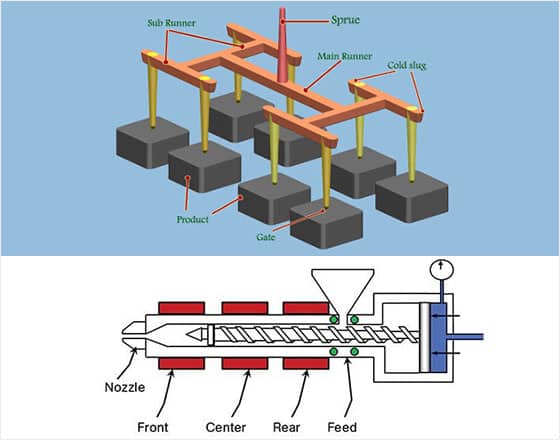
3.Forming Parts
Forming parts refer to all kinds of parts forming the shape of products, including moving mold, fixed mold, cavity, core, forming rod and exhaust port, etc. The forming part is composed of core and mold. The core forms the inner surface of the product and the die forms the outer surface shape of the product. After clamping, the core and cavity form the cavity of the mold. According to the process and manufacturing requirements, sometimes the core and die are composed of several pieces, sometimes they are made as a whole, and only inserts are used in the parts that are easy to damage and difficult to process.
4.Structural Parts
It refers to the various parts of the mold structure, including: guide, demoulding, core pulling and parting parts. Such as front and rear splint, front and rear buckle template, pressure plate, pressure column, guide column, demoulding rod, return rod, etc.
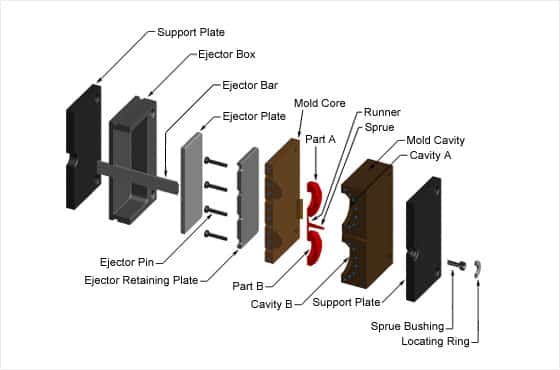
Applications Of Injection Molding
Injection mold is an important process equipment to produce various industrial products. With the rapid development of plastic industry and the promotion and application of plastic products in aviation, aerospace, electronics, machinery, shipping and automobile industries, the requirements of products for mold are becoming higher and higher. Traditional mold design methods can not meet the requirements of today, Computer Aided Engineering (CAE) technology has great advantages in improving productivity, ensuring product quality, reducing cost and labor intensity.
In the processing of injection mold, all kinds of numerical control machining are useful, and the most widely used are numerical control milling and machining center. The application of numerical control wire cutting and numerical control electrical discharge machining in mold numerical control machining is also very common. Wire cutting is mainly used in all kinds of straight wall mold processing, such as concave convex mold in stamping processing, insert block and slider in injection mold, Electrode for EDM. For the mold parts with high hardness, the machining method can not be used for machining, and most of them are EDM. In addition, EDM is also used for the sharp corner, deep cavity and narrow groove of the mold cavity. The CNC lathe is mainly used for processing standard parts of mold rod, mold cavity or core of revolving body, such as injection mold of bottle body and basin, forging mold of shaft and plate parts. In the mold processing, the application of CNC drilling machine can also improve the processing accuracy and shorten the processing cycle.
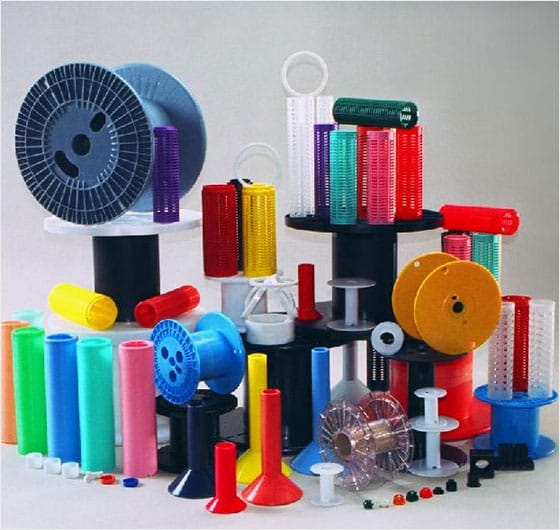