Processes
- Polymer Processing
- Injection Molding Insert Molding Blow Molding Over Molding Metal Injection Molding Thermoforming
- Metal Casting
- Die Casting Castings & Forgings Wax Casting Lost Wax Casting Grey Iron Castings Centrifugal Casting Investment Casting Permanent Mold Sand Casting Shell Mold Casting Aluminum Investment Casting Brass Investment Casting Steel Investment Castings Titanium Investment Casting
- Machining
- Milling Turning EDM machining CNC Engraving Hole-making Tap Size Chart Drill Size Chart 5 axis machining Micro Machining CNC Cutting Metal Processes Ceramic Manufacturing Swiss Precision Machining
Materials
What Is FDM (Fused Deposition Modeling)
Fused deposition modeling (FDM) is a process in which filamentous materials such as thermoplastic, wax or metal are extruded from a heated nozzle, and the melt is deposited at a fixed rate according to the predetermined trajectory of each layer of the part. FDM is one of the most widely used additive manufacturing techniquedue to its cost effectiveness and simplicit, if FDM works with specialized 3D printers and production-grade thermoplastics that can build strong, durable and dimensionally stable parts.
The History Of FDM Development
Fused Deposition Modelling (FDM) is a technology invented by Scott Crump (Scott Crump) of Stratasys of the United States in the late 1980s. It is followed by light curing rapid prototyping (SLA) and lamination After the physical rapid prototyping process (LOM), another widely used 3D printing technology. In 1992, Stratasys launched the world’s first 3D printer based on FDM technology-“3D Modeler”, marking the commercialization of FDM technology.
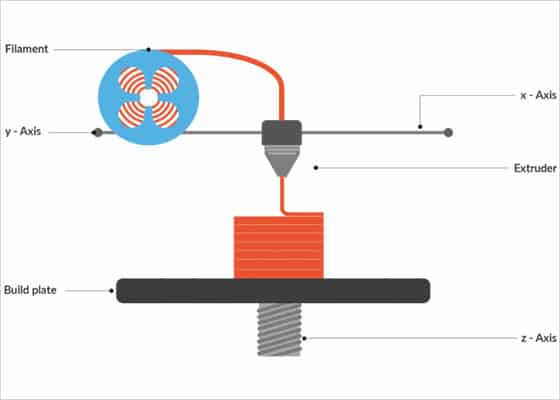
How Does FDM Work?
A roll of thermoplastic filament is loaded into the printer. Once the nozzle reaches the required temperature, the filament is fed into the extrusion head and melted in the nozzle.
The extrusion head is connected to the 3-axis system so that it can move in the X and Y directions. The melted material is extruded into thin strips and deposited layer by layer at predetermined locations where it cools and solidifies. Sometimes, the cooling rate of the material can be increased by using a cooling fan mounted on the extrusion head.
After the printing of one layer is completed, the worktable decreases the thickness of one layer by a predetermined increment along the z-axis direction, and the material is extruded and deposited on the solidified material of the previous layer, and the final product is formed by stacking the material layer by layer.
After printing, remove the support and surface treatment.
Printing time varies on the product being made. Small items—just a few cubic inches—and huge, thin things print rapidly, whereas bigger, more complicated items print longer. Compared to other 3D printing processes like stereolithography (SLA) or selective laser sintering (SLS), FDM is a long process.
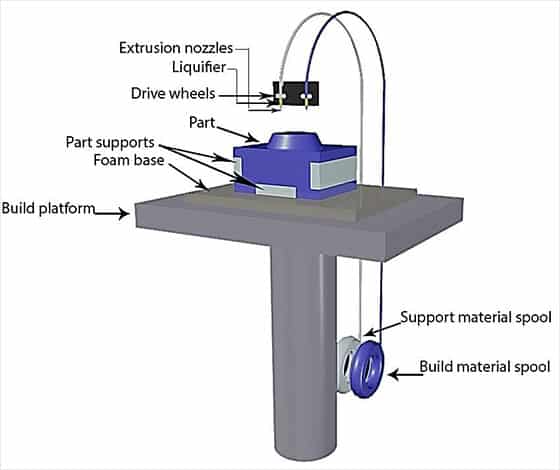
Applications Of FDM
Fused Deposition Modeling is a solid-based fast prototyping approach that extrudes layer-by-layer material for a model. The system is a construction platform, extrusion nozzle, and control system. This is a rapidprocedure for validating designs, fit and function testing, short production runs, jigs, and fixtures.
- Large assortment of materials includes ABS and ABS food-grade
- Short lead times, 3-5 days typical lead time.
- High power
- Highly durable
- Models of concept
- Model engineering
- Functional tests
- Products for consumers
- High-temperature applications
- Original prototypes
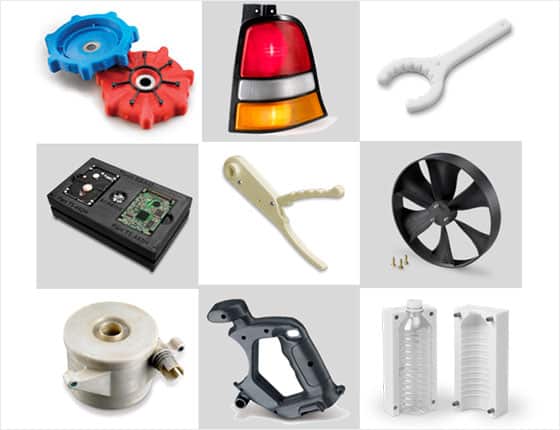
Advantages Of FDM
- FDM is the most cost-effective way to produce custom thermoplastic parts and prototypes.
- A variety of thermoplastic materials are available for prototyping and some non-commercial functional applications.
- The technology is clean and user-friendly.
- Supported production-grade thermoplastics are mechanically and environmentally stable
Disadvantages Of FDM
- Compared with other technologies, FDM3D printing has the lowest dimensional accuracy and resolution, so it is not suitable for parts with complex details.
- FDM parts may have visible layer lines, so post-processing is needed to make the surface smooth.
- Layer bonding mechanism makes FDM parts have inherent anisotropy.
- FDM has low precision,complex components are not easy to manufacture.
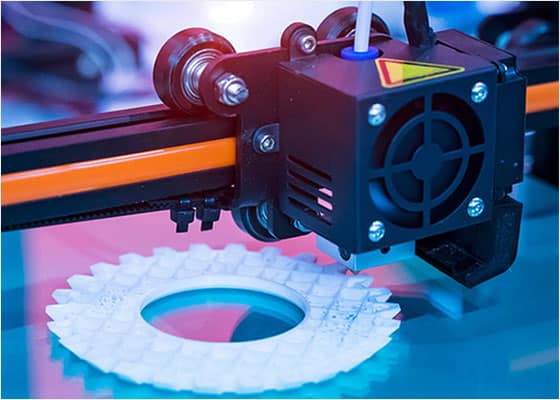
Fused Deposition Modeling Capabilities | ||
---|---|---|
Abbreviation: | FDM | |
Material type: | Solid (Filaments) | |
Materials: | Thermoplastics such as ABS, Polycarbonate, and Polyphenylsulfone; Elastomers | |
Max part size: | 36.00 x 24.00 x 36.00 in. | |
Min feature size: | 0.005 in. | |
Min layer thickness: | 0.0050 in. | |
Surface finish: | Rough | |
Applications: | Shape/fit testing, functional testing, rapid mold patterns, small detail parts, demonstration models, patient and food applications, high temperature applications |