Processes
- Polymer Processing
- Injection Molding Insert Molding Blow Molding Over Molding Metal Injection Molding Thermoforming
- Metal Casting
- Die Casting Castings & Forgings Wax Casting Lost Wax Casting Grey Iron Castings Centrifugal Casting Investment Casting Permanent Mold Sand Casting Shell Mold Casting Aluminum Investment Casting Brass Investment Casting Steel Investment Castings Titanium Investment Casting
- Machining
- Milling Turning EDM machining CNC Engraving Hole-making Tap Size Chart Drill Size Chart 5 axis machining Micro Machining CNC Cutting Metal Processes Ceramic Manufacturing Swiss Precision Machining
Materials
What Is Grey Iron Casting
Grey iron casting (gray cast iron) refers to the cast iron with flake graphite. It is called gray cast iron because the fracture is dark gray during fracture. According to the shape of graphite, gray cast iron can be divided into ordinary gray cast iron, graphite is flake; Nodular cast iron, graphite is spherical; Malleable cast iron, graphite agglomerated flocculent; Vermicular graphite cast iron, graphite is vermicular.
The History Of Grey Iron Casting
Gray cast iron is a casting alloy with a long history. Mankind’s mastery of the production technology of gray iron castings is the beginning of the “Iron Age” in the process of civilization development. It is precise because of the production technology and development of gray iron castings that steam engines and a variety of industrial machinery have emerged, thus promoting the industrial revolution. The Chinese were the first to master the technology of cast iron in the world. The West entered the iron age about 2000 years later. After the industrial revolution, with the development of science and technology, nodular cast iron came out in the 1940s, and various high-performance casting alloys have been continuously developed, popularized, and applied. In the past three decades, the application of nodular cast iron and various light alloy castings has developed rapidly, but gray cast iron has many superior properties. In the current economic development, it is still a very important casting alloy with a wide range of influences. So far, gray cast iron is still the largest casting alloy.
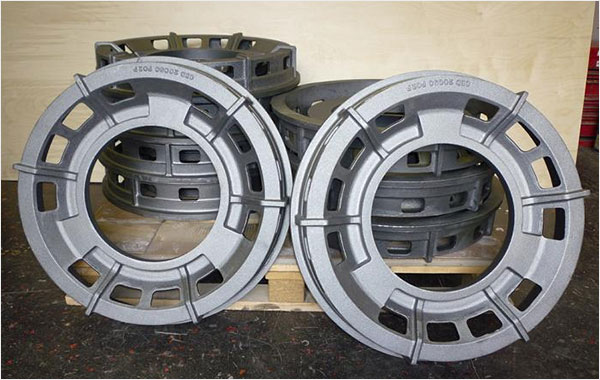
The Applications Or Grey Iron Casting
The main components are iron, carbon, silicon, manganese, sulfur, and phosphorus. It is the most widely used cast iron, and its output accounts for more than 80% of the total output of cast iron. Carbon exists in cast iron in the form of flake graphite. The fracture is gray. It has good casting and cutting properties and good wear resistance. Used for manufacturing frame, box, etc. The graphite of gray cast iron is a flake, the effective bearing area is relatively small, and the stress concentration is easy to occur at the graphite tip, so the strength, plasticity, and toughness of gray cast iron are lower than those of other cast iron. But it has excellent vibration damping, low notch sensitivity, and high wear resistance.
The Advantages Of Gray Iron castings:
- Good wear resistance and shock absorption. Because graphite in cast iron is conducive to lubrication and oil storage, it has good wear resistance. Similarly, due to the existence of graphite, the shock absorption of gray cast iron is better than that of steel.
- Good process performance. Due to its high carbon content and close to eutectic composition, gray cast iron has a low melting point, good fluidity, and small shrinkage. Therefore, it is suitable for castings with complex structures or thin walls. In addition, because graphite is easy to form chips during cutting, the machinability of gray cast iron is better than that of steel.
- Relationship between hardness and tensile strength: There is a certain corresponding relationship between the hardness and tensile strength of gray cast iron. The empirical relationship formula is: A. when o ≥ 196N / m ㎡, Hb = Rh (Fei 00 + 0.4380b)… (B1) B. when o ≥ 796n / m ㎡, Hb = Rh (44 + 0.7240b)… (B2). The relative hardness (RH) value in the formula is mainly determined by the raw material, melting process, treatment process, and cooling rate of the casting.
- Advantages of resin sand casting machine bed castings:
- The resin sand mold has good stiffness and high sand mold strength at the initial stage of pouring, which makes it possible to effectively eliminate shrinkage cavity and porosity defects by using the graphitization expansion in the solidification process of cast iron, so as to realize less riser and no riser casting of gray iron and nodular iron.
- Polystyrene foam pattern is used in full mold casting production, and furan resin is used for self-hardening molding. When the molten metal is poured into the mold, the foam mold is rapidly vaporized and burned away under the action of high-temperature molten metal. The metal liquid takes the place of the original foam plastic, and is cooled and solidified into a solid mold with the same shape.
- Relatively speaking, lost foam casting has great advantages over traditional sand mold in the production of single or small batch automobile panels and machine beds. It not only saves the expensive wood mold cost, but also is easy to operate, shortens the production cycle, improves the production efficiency, and has the advantages of high dimensional accuracy, small machining allowance, and good surface quality.
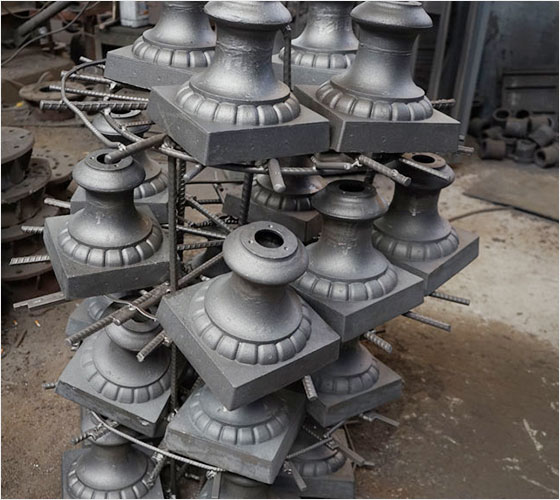
Types of Grey Iron Castings
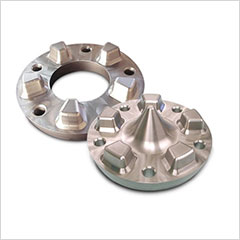
Alloy castings
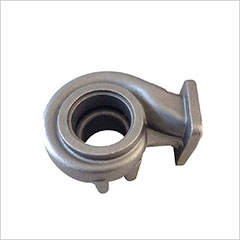
Core processes
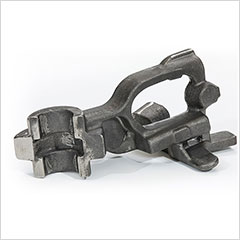
Ductile castings
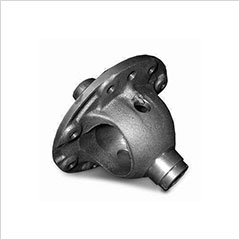
Ductile iron castings
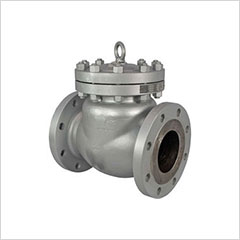
Gray iron castings
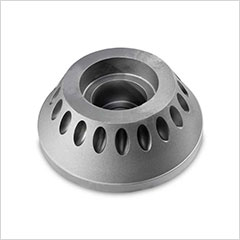
Gray iron
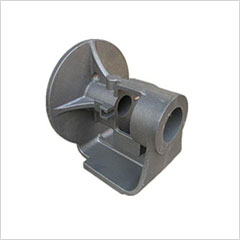
Green sand casting
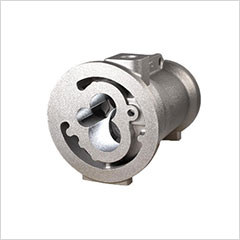
Grey casting
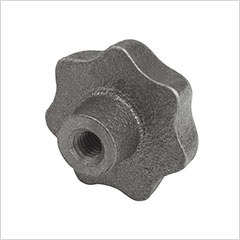
Grey Iron Castings
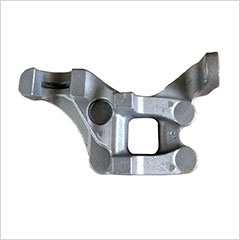
Grey iron casting services
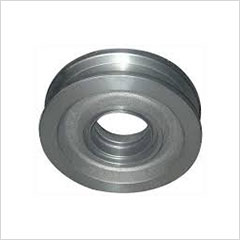
Iron castings
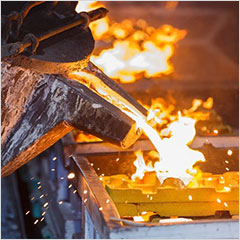
Iron foundries
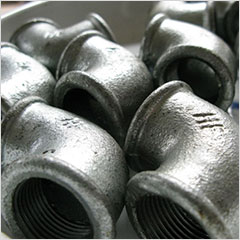
Malleable iron castings
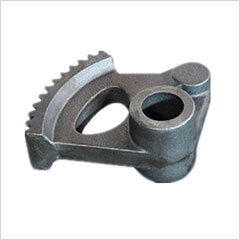
Spheroidal graphite cast iron